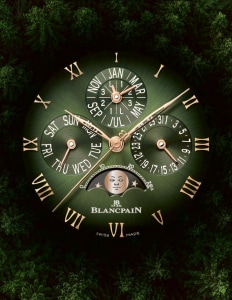
Chapter 2
An intimate look at complicated watchmaking
There are places that watch lovers dream about, among them the manufacturing workshops where watches are born. The manufacture blancpain, nestled in a landscape alternating between lush and snowy white, has exceptional capabilities when it comes to making watches. For evidence of this, all you have to do is enter through the doors of the minute-repeater workshops. Then look and listen carefully, for this is the holy of holies, where the music of time is written and heard.
At a watch manufacturer, the complications workshops are a privileged zone where exceptional skills are brought together. Many watchmakers, even the most junior, dream of working there one day. It would be the high point of their careers. And in the world of complications, beyond the tourbillons, perpetual calendars and equations of time, one workshop reigns in isolation above the rest. It’s where they make the minute-repeaters. Enter this sanctuary on tiptoe; hold your breath and you might hear the gentle strike of the hours, quarters and minutes.
Dong! Dong! Dong! Dong! Ding-dong! Ding-dong! Ding! Ding! Ding! Ding! Ding! It’s an ancient melody from an unelectrified age when the pocket-watch on the bedside table told you the time without you having to light a candle. The fortunate owners of these mechanical and acoustic marvels had only to slide a bolt on the watchcase for the minute-repeater to deliver its message of sound. The format has not changed: the hours are struck in low notes, the minutes are sounded in high notes after double strikes of high and low notes indicating the quarters. You thus have to count the number of hours struck (4), add the two quarters (half an hour) and then the strike of five minutes to arrive at a time of 04:35—rather too early to get up.
Ready in Five to Six Weeks
In Le Brassus, the complications workshops comprise 18 people under the responsibility of Mustapha Ahouani. This Frenchman of Moroccan origin is a complete watchmaker if there ever was one and can carry out practically every watchmaking task. Even the most complicated watches that come into his hands hold no secrets from him. The average age of his team members is 33 to 34 years old, the youngest being 25: ”It’s a young age to be working in the complications workshops because you need a lot of experience to cope with these kinds of mechanisms. However, it is possible. It all depends on the individual, their abilities, skills and motivation. In any case you have to be enthusiastic. You can take five or six weeks to make the product, sometimes longer. You need a lot of patience and dexterity. And to get this far you also need to have come across the right people throughout your training period.”
From the Baseplate up
His deputy, Laurent Salomon, agrees, convinced that he too has made the right contacts at the right time. The people who transmit the virus, take you in their trust, give you the opportunity to develop and make you want to go further, are of the greatest importance because it’s all about handing down knowledge and skills. Laurent is in charge of the minute-repeater and he cannot say enough about the subject. How does a watchmaker get to work on the queen of complications? “It’s a long process. You start by putting together a simple movement, and you progress carefully to adjusting the watch. Then you tackle the additional plates, for the simple date, the annual calendar and the perpetual calendar. Then you go onto the tourbillon and maybe to the running equation of time. When you get to the repeating mechanisms you’ve reached the top. Places have to be earned in this specialty because there are few companies in the watch industry that really make repeaters from A to Z. We’re fortunate here because we build them from the baseplate up.”
All in all, six watchmakers at Le Brassus are involved with minute-repeaters in different capacities. Four of them—Romain, Félicien, Laurent and Michaël—handle production, while Norbert ensures the after-sales service and the sixth member, Georg, also works in aftersales, but specifically on the supercomplicated 1735 model. Only 30 of these watches were made, but maintaining them understandably takes time, indeed the whole time of an ultraspecialized watchmaker. “Unfortunately, some clients treat them as if they were sports watches, and they are not waterproof,” Mustapha Ahouani points out. “They sometimes come back completely rusted inside and they take six months to be restored. We have the same problem with the so-called simple traditional minute-repeaters, where water-resistance was not an objective—except for a few small series—which seems reasonable if you want a better sound quality. We achieve this with our latest caliber, but you have to consider that a sealed case for a repeating watch is much more difficult to realize.”
Tightly Knit Team
The team is small and tightly knit. If you go by its rate of production, the nature of its task, the care taken in the slightest detail, not only for its own sake but also for essential functional reasons, you find yourself in a bygone age. That impression is strengthened by the fact each piece is built from scratch, which is today rare among watch manufacturers. The concept is not without interest, and if the advantages are apparent, so are the drawbacks of working in a time capsule. But the fact remains that if a minute-repeater fashioned entirely by a single watchmaker is a guarantee of its quality, the methods involved are incompatible with the widespread search for productivity.
Each craftsman has his knack, his style and his ear; thus every minute-repeater is in a way unique. Does that mean its creator will recognize it when it returns for a service? The head of the complications workshops answers with a smile: “The watchmaker who assembled it will recognize it for sure. Yet on the whole it won’t be any different from another. What we emphasize here is a consistent process, methodology and the handing down of knowledge that sets out and explains what you have to do in each operation from the assembly of subcomponents to the final casing up. The basic work has to be identical. Thereafter you will find the watchmaker’s personal touch, in a decoration for example or in the various widths of a chamfer.”
Ensuring the Survival of Skills
The purpose of this approach based on dialogue and the exchange of ideas is to ensure the consistent and unfailing quality of all the watches, and to sustain the uniformity of production right to the top of the pyramid. It’s also a way of keeping skills alive beyond the product. The mentality in the workshops has changed. In the old days, everyone guarded their little secrets, which they took with them into retirement. Today the secrets are uncloaked and the order of the day is the sharing of knowledge, information, observations and ideas. “There are no longer any secrets,” declares the head of complications. “Sharing knowledge in a small team creates trust and a spirit of cohesion and harmony that undoubtedly contribute to the quality of the end product.”
After-Sales Service, the True Measure
The production of complicated watches and their after-sales service are closely interwoven in Le Brassus. There are several reasons for this. The after-sales service is the absolute measure of the quality of workmanship delivered. It is a mine of very useful information that enables watchmakers to constantly improve the quality of their pieces, develop a caliber or model and to bring them to life. When a product is sent back, it doesn’t necessarily mean an assembly error. It could also indicate a fundamental technical problem in the design itself. Or else it could be the result of wear, which might involve the type of material selected.
The real life of a watch on the wrist over time is the most unforgiving of tests. Analysis and diagnosis by the specialists in the complications workshops provide the information going back all the way upstream and enable the constant improvement of new products.
The production and after-sales service are closely intertwined for another practical reason. The work is organized to this purpose and demands flexibility from the complications watchmaker. The Blancpain production facility in Le Sentier provides him with a kit of all the parts he needs to assemble the caliber in his care from A to Z. The job will take him one or several weeks, depending on the caliber, and five or six weeks for a minute-repeater. He will immerse himself completely in his task, calmly and steadily going through each stage with the concentration demanded by these high-grade mechanisms. But if there’s an emergency he will put his production task aside to meet the more critical demand. “When a recent model that’s still under guarantee is returned, then we have to react fast so we can give the client his watch back as soon as possible. Often it’s a trivial matter. It could be a technical problem or damage because the watch has been dropped.”
The repair times vary of course according to the type of work needed. “Typically, as in the case of a Le Brassus Carrousel Répétition Minutes model that we received today, we estimate that it will take a couple of weeks, including the technical verifications, inspections and checking the power reserve. Paradoxically, for this type of product, the watchmaker will spend far less time working on it—three or four days—than the time subsequently taken to carry out the checks.” Service quality comes at this cost, and the verification process is essential. This means that sometimes the clients have to champ at the bit, but if they are true aficionados they will understand what’s involved in this service. Nevertheless, the main rule is that the watch must be returned as soon as possible, perfectly repaired with the case cleaned and polished so that the owner once more experiences the same thrill of buying a new watch.
The North Face of the Eiger
Why is the minute-repeater such a difficult complication to deal with? Whether it involves building one or repairing it later, it is always put into the hands of a seasoned and experienced watchmaker. In the end, as in the case of the Le Brassus Carrousel Répétition Minutes, it has to turn out as a well-adjusted instrument of 450 perfectly functioning components. Of course, not everyone can do the job. Every watchmaker knows this and has a deep respect for the professional performance of the specialists in this complication. Similarly, alpinists and mountain guides esteem those who tackle the north face of the Eiger as true connoisseurs.
Behind each delivered watch has been an adventure that takes over the mind of the craftsman for emotion-packed weeks of deep satisfaction and disappointments. There are so many difficulties to overcome, involving going back a hundred times over the same work, dismantling laboriously constructed mechanisms, building them up again, and readjusting everything. That is the way of the game, but it is not always easy on the mind, as Laurent recalls: “ Sometimes I used to get home in the evening in despair and tormented by the problem to be solved. But with experience you realize that you always end up finding the answer, so you put the problem in its context and it becomes easier for those around you. We don’t show it, but in our hearts we continue to think about it. I expect that applies to all of us in the workshop. We all dreamed of doing our jobs at this level, we are all committed and perhaps we pay the price—but with no regrets.”
The Major Difficulty
The main difficulty of this great complication that combines a watch mechanism with a chime, resides not only in the number of parts but also in their nature and size. The basic challenge is to sustain such intricate and complex machinery within the dimensions of an elegant timepiece that can be worn on the wrist. But how does it work? The basic principle is that when you want to hear what time it is, you push the sliding bolt that you can see on the caseband of practically every minute-repeater. By doing this, you load a spring that, when released, provides the energy for the chime to play its part and compose its message in sound. It must be remembered that the minute-repeater takes no extra energy from the basic movement, leaving it free to power other, often associated, functions. The movement can be manually wound or selfwinding and feature a display of automatons.
Feeling Right
With your thumb, you have thus provided enough energy for the chiming mechanism, which uses it immediately to activate the hammers that strike the gongs. However, to do this properly and to strike the gongs the right number of times to the minute, the true time has to be found mechanically. This is the role of the feelers, thin levers that drop on the star wheel and snail cams for the hours, quarters and minutes that rotate according to the time. As the specialists at Blancpain’s describe it: “A minute-repeater is a matter of angular movements. The feeler has to move through wider or smaller angles according to the time to be struck.” This maneuver takes less time than it does to describe, because as soon as the bolt is released the repeater starts striking the hours, quarters and minutes.
This mechanism is extremely tricky to construct because it demands absolute precision and the components are very delicate. The parts in the kit come into contact when they are assembled. “We adjust them together to achieve the minimum amount of play between them.” But why can’t they be made to the right size in the first place? “That is not possible because at that scale we are at the production tolerances of more or less so many microns. The final adjustment of each part has to be done by removing the right amount of material by hand, piece by piece.”
The Gift-Pack of Components
The watchmaker who assembles minute-repeaters has a panoply of files of various fineness as well as a number of specific tools that are not used for ordinary watches. All the components are systematically burnished, a process that hardens the metal so that it doesn’t wear out prematurely. “If we didn’t burnish the gathering pallets, for example, they would break after ten goes,” Laurent Salomon declares before going on to describe the various assembly stages, starting with the gift-pack of parts from Le Sentier. The parts are initially checked, although some of them, like the bridges for example, have already been decorated and will not be altered by the watchmaker. He will nevertheless be responsible for the straight-graining or chamfering of the other parts after having made the three-dimensional adjustments
The job starts with an assessment of the surfaces of the springs, followed by the assembly of a mechanism such as the governor for the striking rate. The aim is to achieve the minimum amount of play. The watchmaker then goes on to assemble another mechanical complication, followed by another, and so forth. The parts are polished in turn, each with a special paste according to the material it’s made of.
Build and Dismantle
Sometimes a sub-assembly has to be rebuilt, for example when it doesn’t fit properly in the next stage of assembly. Then you have to dismantle it and start over. The process is carried out with extreme care in successive steps.
Every time a component of a minute-repeater is fitted, it has to be adjusted. “With the gathering pallets for example, the holes are always smaller than the shafts and the watchmaker has to make them fit. There is always some material to be removed, so that he can adjust the right amount of clearance for the best security. The same goes for the star wheels which are corrected with a very precise reamer to the nearest micron.”
It takes almost a week to put together all the sub-assemblies. Then comes the assembly of the movement as a whole, which involves putting together all the pre-assembled components with the winding stem, the pinions, the setting wheels and the adjustment of all the “dry” clearances, for at this stage nothing is yet lubricated.
The next stage involves the balance-wheel fitted on a spring with a Breguet overcoil. After the going train is put into place and oiled, the basic movement can be adjusted, fitted with a date, a tourbillon, whether manually wound or selfwinding. Once the rate of the movement is within the limits in the six conventional timing positions, the watchmaker can at last tackle the most interesting part—the mechanism of the minute-repeater itself.
The World of Sound
Three weeks have already gone by and the assembly continues. The components are now adjusted against each other one by one. This is referred to as assembly “in the gray,” fitting all the elements to the correct clearances and amount of play.
Ding! Dong! Between each strike there must be a gap of at least two gong strokes: that’s the rule. The pitch of the note depends on the length of the gong. So you can guess that it’s a matter of cutting it down to size. “We are not trying to play any particular note,” Laurent points out. “We aim for the right gap between them. When we have that we can start tuning the gongs.
The gong must be able to vibrate freely for a crystal-clear sound. A tin-pan noise is unacceptable. We also have to give the chime enough volume.” To achieve this, the gongs, which are curved steel rods, are filed at the base of the holding blocks to which they are welded. The quality of the weld is crucial; it has to be impeccable. Similarly the gong-holder must fit perfectly against the movement and be absolutely level. The screws must also be without blemish because when it comes to sound, excellence is in the details.
The so-called cathedral gong is distinguished by its length. While ordinary gongs are somewhat short of the circumference of the movement, cathedral gongs go around it one and a half times at least. The result is a much fuller sound. And should the sound be a little dull, the pinning-point of the gong is cut off at an angle.
When all that is done, the movement is fully dismantled, washed, reassembled and oiled. It will be fitted with hands and cased up. Tension runs high. The minute-repeater has been listened to with attentive ears before being cased up. It will be heard again within its case— a completely different environment—and this major step can always bring more surprises. A problem with the hands or a false note means that it has to be done over again.
Nothing is sure until the last moment, there are no short cuts. The watchmakers in the minute-repeater workshops know this from experience. Yet they accept this uncertainty as one of the glories of their craft.