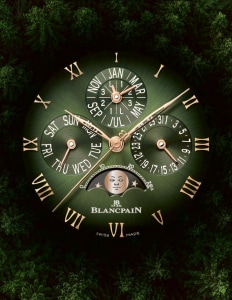
Chapter 4
Exploring the details of crafting a finely made watch case.
You have to hand it to the fraternity of watchmakers. They bask in adoration coming from all quarters. Magazines, social media, the internet placing them and their handiwork on pedestals. Through it all, spotlights have been trained on their établis (workbenches) revealing their methods, techniques and, even on occasion, secrets. In a word, collectors know or at least think they know how movements are built and how watchmakers work. But what about case makers? Without doubt connoisseurs scrutinize the smallest details of design and finish and rejoice upon seeing and, yes, feeling an exquisitely finished watch case. Of course they should. In some ways, there is a tighter bond between a watch owner and his watch case than there is with the movement.
After all, even with an open case back, the movements are generally hidden 100% of the time when the watch is being worn. But the case of the watch fully puts itself on display 24/7. That said, although its virtues vividly present themselves and are well admired, what about the processes and people
that produced it? Manifest unfairness, for this all important aspect of watchmaking has largely been relegated to obscurity, hidden behind a veil. So let us pull back that veil and explore the fine art of
case making.
Many art forms embellish. What began as a canvas remains a canvas. Same for engraving. An engraved object retains its core essence. Case making on the other hand is transformative. A raw bar of metal, be it gold, platinum or steel, is transformed into a voluptuous sculpture. Gazing at the flowing curves and glimmering polish it is difficult, bordering on the impossible, to imagine that a Blancpain case was once a charmless hunk of material. What is remarkable is that, seen from 10,000 meters, the art of this transformation has remained basically the same for two centuries. Machines are employed to arrive at the basic shape of the case, followed by painstaking hand work to bestow the finish. This is not to say that the machines have not evolved over this time. Of course they have. That said, a visit to the workshops of a sister company commonly owned with Blancpain, Simon Et Membrez, located in a remote corner of the Swiss Jura in the town of Delémont, where Blancpain cases are crafted, always begins with a tutorial on the methods from the past.
Polishing a Blancpain double stepped bezel requires enormous skill, as, on the one hand, a perfect sheen must be bestowed upon it and, on the other hand, the sharp border must be preserved.
There is a striking link between the history of case making and the making of movements. In the same way that farmers in the Swiss Jura spent the winter months on the upper floors of their barns, working above their cows, fabricating movement components, case makers practiced their unique craft in similar circumstances. The basic form of their cases was achieved through a cutting, followed by a carving process, both utilizing hand powered spindle machines. Around the end of the 19th century, case making moved from the farm to the factory. Interestingly, it was the Americans who initially provided updated tools for the machining steps. In the early 20th century, the Swiss deve-loped the next generation of tools. These Swiss machines drew their power via belts connected to overhead pulleys, and, working upon round disks of metal, carved the round details of the case with a battery of specially shaped awls (called burins). These machines were fitted with a variety of differently shaped burins, each shape designed to carve a particular element of the case. The method at the time called for pressing the case against the fixed point of the selected burin and turning it against the tip, with the depth precisely set via a control. Naturally, since the tools were conceived to shape the round elements of the case such as the bezel (interior and exterior), interior supports for the movement, case back and other fine elements, the lugs, most decidedly not round, were soldered in place at a later stage.
Further advances came later in the course of the early 20th century. Machines were developed powerful enough to stamp bars of gold, steel or platinum into the basic shape of the final case, including the lugs. After the stamping, carving and hand finishing processes would follow.
Today’s methods represent yet a further evolution of this historical progression. First, of course, is finalizing with high precision the design of the case in every single one of its details. Some of these details are largely visible: the bezel, the fitting of the crystal, the interior ring above the dial, the flow of the case to the lugs, the case back. Many, however, are not as visible: the interior flanges for the movement, cut-outs for Blancpain’s exclusive patented under-lug correctors and their connections to the movement, openings for the crown, the fit of the dial into its opening, the clearance of the winding rotor, elements such as chronograph pushers and much more. Even though detailed drawings are developed by Blancpain’s design teams for all of these particulars, there is often considerable back and forth technical discussion to ensure that the case can be produced to perform as designed.
A historic Güdel case carving machine.
Polishing the lugs.
Once the design is finalized and approved, for most Blancpain cases, stamping represents the first production stage. However, before that can begin, the stamping tools must be fabricated. There is a veritable library of tools, unique for every Blancpain case, filling special shelves at Simon Et Membrez. As much as 200 tons of force are brought to bear to stamp the form of the case with its lugs. This first stamping produces a stark, straight-sided shape. In the 1950s the immediately following steps would be machining to create the finer elements of form. As machining away material, even if most of the fine grains are recovered, is inevitably somewhat wasteful, the first stamping is now generally followed by additional stamping steps instead of proceeding immediately to machining. There can be as many as twenty successive stampings, each targeted at a particular element of the case shape, with each stamping separated by a complex heating/cooling process. The reason for the heating, done in a hydrogen atmosphere, is to condition the gold or steel for the further shaping to follow.
Elaborate carving steps follow the stamping. For round elements, today’s machines, although highly advanced and programmable, operate in a similar manner to the pulley-driven burin machines which debuted in the early 20th century. The process is called tournage (turning). The tip of a burin, which performs the carving, is fixed into position, and the case is pressed against it and rotated. As with the historical pulley machines, there are a variety of burin shapes, each one targeted at a particular case element. Keep in mind that for a Blancpain case, these steps are followed not only for the main body of the case, but the bezel and the case back as well. Although the core idea of carving with a burin has carried over from the earlier pulley machines, one aspect of today’s process has advanced enormously: precision. For their time, the pulley machines achieved admirable precision with vernier adjustments allowing for tightly controlled depthing of the tool. Now, however, Blancpain’s case elements can be carved with a tolerance on the order of 3 microns. This becomes extremely important, to cite three examples, to ensure proper fitting of the bezel into the flange carved into the case body, the fitting of the sapphire crystals into the bezel, and the fitting of sapphire onto the case back.
For some models, the elements of the case are so complicated that an array of different burins in one machine is not enough. A good example is the Villeret Calendrier Chinois Traditionnel. Three separate machines, each with a selection of burins, are required to perform all of the tournage operations.
Machines similar to those which are used for tournage perform drilling of holes, which is termed fraisage.
A moment of thought quickly yields the list of holes found in the case: the crown, pushers for chronographs, correctors for those models which do not have correctors under the lugs, the interior of the lugs for the spring bars that hold the strap.
Thus far, all of the operations have been aimed at creating the basic shapes of the case (and separately the bezel and case back) and its internal and external elements. But we are only a fraction of the way on the journey toward completion of the case. What remains are dozens of hand-milling, engraving,
finishing, and assembly steps. Hopefully with a Blancpain timepiece close at hand, let’s take a tour of the case and consider some of the hand operations which have been performed.
A good place to start is with Villeret case lugs. The form of the case body adjacent to the lugs slopes slightly inward toward the case back. Yet the intersection of the lug and the rounded body is crisp and sharp. Achieving that finely drawn junction calls for hand milling. Traditional round mill stones are used. With both practiced eye and touch, the case maker forms the fine edge of the junction on the edge of the turning stone. The inside intersection of the lug and case body is formed in the same way.
In between successive stamping operations, the cases undergo a heating process.
Polishing is its own art form. Working under specially calibrated lights, conceived to highlight even the most miniscule flaw, the case makers progressively address every surface on the case body. A succession of ever finer brushes and lighter abrasive materials are used to arrive at a perfect sheen. Matters are particularly delicate at the joint between case body and the lugs. All the care lavished upon those intersections at the milling wheel could easily be compromised with mis-performed polishing. Only the most talented case polishers are able to preserve fully the sharpness of junction while at the same time extracting the fine luster that is the mark of a Blancpain case.
Blancpain’s signature double pomme bezel poses its own special challenge. Here again it is a junction, that between the two rings of the bezel, which calls upon special skills. The case polisher fits the bezel on a custom designed holder and carefully addresses the junction with a finely edged polishing brush. Not only must the edge retain its sharp definition, but the form must be consistent around the full 360-degree circle of the bezel. Only master craftsmen with years of experience are tasked with this finishing step. Of course, the other surfaces of the double pomme must be po-lished as well and the demands are similar: preserving the perfect form and bestowing the same degree of polish all the way around the rings.
After the polishing operations are completed the components are sent to a different case specialist for inspection. Working under lighting that shows no pity, every surface is closely examined and, if even the smallest imperfection is found, the piece is sent back to be redone.
Not to be forgotten is engraving. Two types of engraving are generally performed. The Blancpain legend, in a relatively large font, is engraved with a cutting tool. So, too, is the case number. Smaller fonts such as those used for the word “Swiss” or the reference number are engraved using a laser.
Careful handwork marks the polishing of case elements.
Depending upon the model, there are special additional steps. Many of Blancpain’s complicated calendar timepieces are equipped with its exclusive under-lug correctors. As the name suggests, these are nestled into a recess under the case lugs and replace the case side dimples which are used industry-wide by others. Not only do these correctors enable Blancpain to create case sides which are perfectly smooth, un-marred by corrector dimples, but they allow the owner to set the calendar indications using a fingertip instead of a push pin tool. The operation of assembling the under-lug correctors closely resembles movement assembly by a watchmaker. The slots and grooves for the correctors are cut into the case before it arrives at the bench of the assembler. The system has several components, the most important of which are the small pusher which nestles under the lugs, a spring assembly which mates with it, and a miniscule keeper (romantically called the crevette, which translates to “shrimp”). Some watches have as many as four correctors (although the Calendrier Chinois Traditionnel and the Équation du Temps Marchante have five), each of which is assembled by a specialist.
Fifty Fathoms pieces have their own special processes associated with the rotating bezel. Various types of bezels are used in the Fifty Fathoms collection: bombé (domed) sapphire and, for the Bathyscaphe models, different bezels with ceramic inserts and Liquidmetal® hour-markers. The sapphire bezel rings arrive at Simon Et Membrez, finished in shape, but lacking color or index markings. The first step is the application of color to the underside of the bezel. The placement of color underneath the bombé ring brings a unique luster and allure to the bezel and is a technique pioneered by Blancpain. After the color is applied, the indexes are laser cut and filled with Super-LumiNova®. Again, all of this is done on the reverse side of the bezel. Mating the sapphire to the bezel ring is extremely difficult as the tolerances of the fit are extraordinarily
Assembly of Blancpain's pattended under-lug correctors.
Assembly of the Fifty Fathoms bezel.
fine. In addition, positioning is exacting. There are fine teeth which are built into the underside of the metal ring which serve to ensure that the bezel rotates in precise small increments. The difficulty that arises is in the placement of the index at 12 o’clock. It must be placed in a position relative to the teeth below such that it will be perfectly centered as the bezel is rotated to the 12 o’clock position. If the relationship between the bezel index and the teeth is not perfectly correct, the index will come to rest either slightly before or after 12, which is unacceptable.
Somewhat in a category by themselves are those Blancpain cases made of titanium. Titanium is extremely hard, presenting unique challenges for machining. First, is wear of the tips of the burin. After only a handful of processes, the tips become sufficiently dulled that they must be replaced. Second, and even more forbidding, is heat. Both machine and components become extremely hot during machining, creating a not insubstantial risk of fire. Thus, special precautions must be taken in those areas where fabrication of titanium takes place.
To walk through the case workshops following all of these processes, and it is no exaggeration to say that there are dozens and dozens of stages for the creation of a single type of case, is to see a Blancpain case with new eyes. Now gazing at the lugs as they flow onto the side of case, inspecting the flawless double pomme bezel or feeling a Fifty Fathoms bezel smartly click into place with index precisely centered at 12, calls to mind the towering savoir faire of the craftsmen in Delémont. •