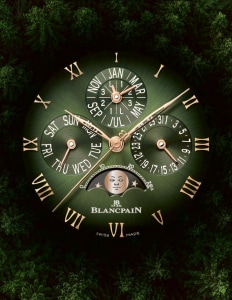
Chapter 4
The best way to imagine how a fine bracelet is constructed is to think of complex Fine Watchmaking.
Villeret Quantième Complet.
Five hundred and thirty-one individual parts. Artisanal assembly by hand and fine finishes meticulously applied by craftsmen. Sounds a lot like the realization of a grand complication movement. It’s not. It is a description of Blancpain’s Mille Mailles steel or gold bracelet. But if the description planted the image of complex fine watchmaking, cling to that thought because it is entirely fitting to the creation of a refined bracelet.
In the hand the Blancpain Mille Mailles bracelet reveals little of the complexity of its design, much less the elaborate steps followed for its construction. Nor should it. Above all else, an haut de gamme bracelet distinguishes itself by all the things it is not: not a trace of ill-fit on the wrist, no hitches in its flexibility, no disharmony in its finishes, no imbalance in its weighting, no gaps in the flow of its elements. If any thought is provoked by the bracelet, it certainly must be along the lines of “how can any metal object be this supple and sturdy at the same time?”
On the wrist or in the hand, the bracelet’s shimmering fine finishes do not reveal its secrets. Although not readily apparent when worn, in fact its construction is complex, requiring studied arrangement of a mixture of eleven different interior and twenty different exterior links, which in French are termed “maillons”. Even close visual scrutiny teases out but a fraction
of the differences. Only when given the opportunity to observe its assembly or study the drawings, does it clearly emerge that not all the maillons are the same and that there are in fact 31 distinct types and sizes. Not surprising that it is this difficult to catalog the differences, as they are subtle often on the scale of fractions of a millimeter, requiring an eagle eye even when they are compared side by side with one another.
Also hidden is the manner in which the components are attached to each other. The maillons are threaded together with fine pins, anchored on each side and running across the bracelet through the interior of the maillons so as to create joined rows. The links are thus invisibly held in place, but free as a connected element of a row to rotate so that the bracelet can form to the wrist.
Notwithstanding having a full understanding of the basic principles of its construction, fortified by close inspection including examining the way in which bracelet flexes, the painstaking processes of assembly and finishing are far from being revealed. To pierce the mystery of how these more than 500 components are brought together requires a trip to the far north of Switzerland, near the French border, in the town of Delémont, where Blancpain’s sister company Simon & Membrez is located.
Of course, the process begins with the manufacture of individual components. Tolerances are microscopic, on the order of 5 microns. Although that sounds extreme, this high precision is required if the individual maillons are to fit together seamlessly and flex freely. The components arrive at the work bench of the assembly specialist already sorted by type, each one in a small numbered bin, the number indicating its type. Keep in mind there are a total of 31 different sizes and types of maillons. Numbering the part bins is important as, only in the case of the unique maillons that include screws so that they can easily be removed with a screwdriver to fit the bracelet to the owner’s wrist, are the types of maillons easily distinguished from one another.
The first step is to fix to the side maillons the pins that run across the width of the bracelet, forming the rows. Each pin is firmly held in place by both the tightness of fit into the drilled hole and glue.
Nothing is left to chance. Even though the pins are double secured—tight fit coupled with glue—the glue itself is tested. When each new batch of glue arrives, a sample is used to fix a pin to a maillon and the force required to pull it apart is measured. Of course, that force far exceeds anything that the bracelet would be exposed to in use. Once validated by the test, the glue of that batch is put into use for production.
When the gluing step is completed, these side maillons, now with pins securely attached, are arranged and ordered by size as they would be in the finished bracelet. The specialist then threads each of the eleven differently sized interior maillons onto the pins. Placing the correct maillons at each location is critical. Generally, a given row will all be of one size, but there are exceptions in the case of the four rows that are removable with a screwdriver (those with screws on the outside to facilitate sizing). These sizing rows have a mixture of two different types of interior maillons. To aid in the process, there is a special tool to hold the assembly, with each location numbered so as to correspond to the particular size of maillons called for at that position on the bracelet.
Once all the interior maillons have been threaded onto the pins, then the second outside maillons are fitted. The system is the same as for the first side: firm fitting into the drilled hole and glue.
At this point the bracelet is largely assembled. It only lacks the component which fits to the watch case at one end, and the buckle at the other. Blancpain requires that its watchmakers attach the bracelet to the timepiece, so the bracelet is sent to the watchmakers with that component, called an “attache boîte” separately. The buckle is attached to maillons at each end, much like the screw system for the removable rows. Although assembly may be completed, short of the steps to attach the bracelet to the timepiece, fabrication is far from over. Finishing awaits which presents its own unique challenges.
To start with, bestowing a perfect sheen on the maillons within the extraordinarily restricted confines of the spaces between each row demands special techniques. The finisher bends the bracelet back on itself row by row to expose to the maximum the interior sides of the maillons. With the bracelet bent back, each side of the space between rows becomes accessible. Each pair of rows is then pressed onto an extra thin rotating polishing brush bearing the romantic name “la brosse moustache” (the moustache brush). The narrow width of the “moustache” is conceived to allow its bristles to work in the restricted space between the rows. This process is repeated for each pair of rows, one by one. When each and every row has been polished with the “moustache”, all of the interior spaces will have been brought to a perfect sheen.
The next step is to address the sides of the bracelet. Here there are two important issues. Obviously, a perfect sheen is required, but so, too, is preserving the perfectly flat surface. Studied technique is called upon to satisfy both at the same time. The bracelet is placed flat upon a supporting platform, and then pressed sideways upon the flat side of a polishing disk oriented at right angles to the bracelet. Thus, the entire side is polished against the flat surface of the polishing disk, bestowing the finish while maintaining flatness.
Once the sides have been addressed with polishing against the flat disk, the finishing work returns to the top surface and further sheens for the sides. A series of three different polishing brushes are utilized, each one successively softer. As the work proceeds from brush to brush, the polishing compounds are changed as well, with each stage employing progressively finer compounds. Although the final polish for the sides can be accomplished by sliding the side against the three different polishing brushes, the top surface demands a row by row approach. In similar fashion to the technique employed with the “moustache”, the bracelet is folded over upon itself so that only a single row is pressed against the brush. Starting from the outermost row, the polishing against the succession of brushes moves successively over the full length of the bracelet.
This leaves the back surface. Here instead of brilliant polish, the aesthetic calls for a satin finish. Satin finish presents its own unique challenges. First the extraordinarily fine lines that are the essence of satinage are achieved by moving the bracelet back and forth against the abrasive wheel. Great care is demanded to ensure that the lines, running lengthwise, are perfectly straight and consistent. Making the task even more demanding is the presence of two small brilliantly polished areas on the back side: the first at the far end of the bracelet, the second a fine border running lengthwise at the far outer edges as the back curves upwards to the sides of highly polished maillons. These two brilliantly polished zones are applied after the satin finish. For the end piece, in order to hold the bracelet precisely correct against the polishing wheel, a paper clip is used so that the border between brilliant and satin will be accurately placed. Equal skill to expose only the to be polished zone to the wheel is called for in the bestowing of a sheen on the narrow zone where the back transitions to the sides of each maillon.
What remains is a final pass through an extremely supple polishing brush, oriented in two directions so as to guarantee that there are no polishing lines on the brilliant surfaces. This is followed by cleaning. Each bracelet is then meticulously inspected under special illumination to verify perfection.
Although the Mille Mailles bracelet is comprised of the greatest number of components, the assembly and finishing of Blancpain’s other styles of bracelets, the legendary 71 bracelet and the Bathyscaphe bracelet, proceed along generally similar lines. Aficionados of Blancpain know the long historical lineage of the 71 bracelet that dates back two decades to the debut of the first Flyback chronograph. In an age of sport watch bracelets that were stiff in seemingly all the wrong places and that often failed to conform comfortably to the wrist, the 71 was a revelation. Its flex pattern and fit to the wrist were revolutionary and established it as the gold standard for metal bracelets. Its secret lay in the subtly rounded forms of its links and edge pieces and the positioning of pins running side to side holding the elements together.
Both the 71 and Bathyscaphe bracelets have a brushed finish. Although they are composed of fewer total parts and fewer types of elements than the Mille Mailles, their assembly and finishing are equally demanding. The basic principles of the construction are the same. The elements of the bracelets are connected by pins, tightly fitted and glued to the outside elements, running across the bracelet connecting to interior components, and then fixed to the far outside. The elements of the bracelet are given a first brushed finish before they are assembled. Following assembly unto the pins, the elements are given a final touch up by holding the bracelet against a turning belt with an abrasive matching the desired fineness of the lines of the brushed surfaces. Bestowing this final touch is extremely demanding as care must be taken to ensure that lines are perfectly straight and oriented precisely lengthwise to the bracelet.
Watchmaking in all of its dimensions has always tested those who practice it, to meet the highest standards of craftsmanship. It is, thus, not surprising that fashioning a prestige metal bracelet exists in a milieu analogous to those in which movements, dials and cases are created. •