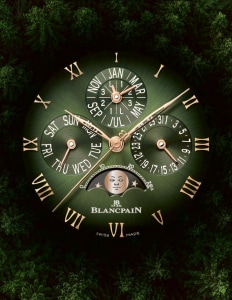
Chapter 6
What watchmakers know and many collectors overlook: the vital importance of equipping a timepiece with the highest quality wheels and pinions.
First a bit of flattery, then for most, a soaking dose of freezing rain. It is almost certain that the majority of the gentle readers of Lettres du Brassus are extraordinarily sophisticated watch collectors at ease in the world of haute horlogerie. And this expertise enables comfortable circulation in this rarified world with a well-developed understanding of the refined finishes of prestige timepieces. Some, without doubt, have risen to become savants eagerly sought out by friends for “watch advice.” But savant or no, how many have devoted themselves with the same intensity of study brought to bear on the visible bridges, plates, winding rotors, balances, etc., to the gears (watchmakers prefer calling them “wheels”) and pinions that are essential components for every mechanical timepiece? Great confidence in putting this forward: unless you are a watchmaker, extremely unlikely.
On the other hand, watchmakers not only focus keenly on wheels, pinions, and the combination of the two, which are termed “mobiles,” they obsess about them. The reason is not only that all mechanical constructions utilize these components, but more than that, the way in which the watch will perform and age depends upon their quality.
All of Blancpain’s wheels, pinions and mobiles are made in the Vallée de Joux within walking distance of both of Blancpain’s two workshops. The manufacture is François Golay, which is commonly owned with Blancpain. Since its founding in the Vallée de Joux in 1855, Golay has specialized in the fabrication of wheels, pinions and mobiles. It is the supplier for es- sentially all of the great watchmaking houses...Vallée de Joux, Geneva, La Chaux-de-Fonds, and Germany alike. One basic to get out of the way: Although Golay is the supplier for this wide industry swath, not all watch houses specify the same level of quality. Blancpain demands the highest grade in the industry and each Blancpain watch is fitted with what Golay terms “haut de gamme” components, the top.
Not only does Blancpain insist upon the highest of the quality tiers, its choice of materials for the wheels sets it apart. In general there are three choices of material which may be specified: brass, German silver, or copper/beryllium. Most watches in the industry utilize brass for the wheels. However, for nearly all of its collections Blancpain has selected the most expensive option, copper/beryllium. Why copper/beryllium? Because it brings added quality to the movement as it is harder, has a lower coefficient of friction and better wear properties than brass or German silver.
The choices of quality level and material, although vital, reveal only a portion of the savoir-faire that is poured into the fabrication and finishing of these key components of every Blancpain watch. The fuller picture emerges with a day spent in the Vallée de Joux in the Golay workshops following the production processes for wheels, pinions and mobiles.
For the wheels, work begins before the first shipment of material arrives. This is because the first step is the fabrication of precision custom tools in order to produce the wheels. Each wheel requires its own special tool,termedan “étampederoue,” which the craftsmen at Golay construct. In one sense the tool storage area of the workshop resembles a library, or better said an historical archive, as arrayed together on the shelves are the individual special tools for each and every wheel that Golay has made over time.
Following the precision fabrication of the tool, production of a wheel can begin. The material for the wheel arrives as a band formed into a large roll, the overall appearance of which is not dissimilar from a huge roll of tape. In the case of Blancpain wheels it is a roll of copper/beryllium. With the custom tool installed on a stamping machine, the form of the center and arms of the wheel are cut into the metal band. For many of Blancpain’s newest movements it is easy to spot wheels in production as the form of the arms, inspired by high performance automobile wheels, termed “à jantes,” is distinctive.
The stamping machines used for this initial step vary according to the thickness and diameter of the wheel being produced. The smallest of the machines stamps with a force of six tons; the largest with a force of 30 tons.
For most wheels, the next step is the precision drilling of the center hole. Here again there are advantages which come from the use of the more expensive copper/beryllium material. To create the center hole for either a brass or German silver wheel, the hole must be drilled. Inevitably, after drilling, there will be a small burr remaining on the lower edge of the hole. With copper/beryllium the hole can be stamped. Stamping brings with it two important advantages. First, stamping can be accomplished with greater precision (on the order of 3 microns) than drilling. Keep in mind that precision is a watchword when it comes to the fabrication of these components. The greater the degree of precision, the better the watch will run. Second, unlike drilling, there is no burr produced on the bottom side of a stamped hole.
There is a bit of romance in the next stage of fabrication as the machine that is used owes its origins to another product far removed from the domain of horology: religious medals! The machine is Italian and it was originally conceived to produce medals in the form of the Madonna. For watch wheels, the “Madonna machine” is used to apply anglage to the arms. The wheels must pass through the machine twice in order to angle both sides of the arms. Once gently angled in the “Madonna machine,” the arms are given a precision polish and gloss as they are tumbled with small particles of nutshells.
Through all of the steps thus far our wheels remain toothless. More decoration remains to be lavished upon them before the cutting of teeth. For most open arm wheels, the next step applies a light circular graining (termed “cerclage”) to both the top and bottom surfaces. Extremely fine sand paper is used for this decorative step. It is interesting that there is a choice to be made on the fineness of the graining. Blancpain selects the finest graining offered. But fineness is limited by what the eye can perceive. If the cerclage graining is too fine, its presence can’t be seen through a clear case back. So the choice is made to apply the finest cerclage that can be seen by the unaided eye.
For Blancpain there are still more decorative steps. Most wheels have a chamfer applied to the center hole. In addition there is further polishing in the form of a mirror finish to a circular band around the center. This mirror polishing is achieved using diamond.
Some components, such as the winding barrel drum receive a different decoration. In Blancpain’s case, the decoration is in the form of fine rays radiating from the center, termed “soleillage.” This is cut into the barrel drum with diamond.
Still no teeth. But with the rest of the finishing work completed, the wheels are now ready for coloring. Barrel wheels will be rhodium plated for most movements. Other wheels will be given a golden coloring, called “dorage”.
Finally, the time has arrived for the element which comes to mind first when thinking of gears, the teeth. For most wheels, the process begins by assembling a group of wheels on a shaft, bounded on either end by “false” or “dummy” brass wheels. Why put a dummy brass wheel at each end of the group? To capture debris from the cutting process on the real wheels. As the cutting tool proceeds down the line of the grouped wheels, cutting debris are accumulated and are deposited on the dummy wheel at the far end rather than on the production wheels in the group. The process is different for barrels, where the teeth are cut for each barrel one at a time.
The fabrication of pinions takes place in a dramatically different way. For watchmakers there are many forms of pinions, but in general they consist of a small diameter gear which is unitary with a shaft. Related are mobiles which combine a small gear which is affixed to a larger wheel. The majority of pinions and the small gears of the mobiles are made of steel, however some may be crafted in copper/beryllium. The process to make a pinion is essentially one that begins with a rod of the material to be used. That rod is fed into a single machine which cuts it into the desired final shape. Thus, if the pinion is to consist of a small gear placed in the middle of a shaft (thus with a shaft on each side), a single section of the rod will be cut, under computer control, to achieve the desired shape; the rod enters the machine and what emerges is a pinion with its gear and shafts on each end, all precisely cut to the correct dimensions and shapes.
Following initial cutting, steps remain before the pinion is completed. First the material must be hardened. The degree of hardness is specified by Blancpain and is met by heat treatment. Following the heat treatment, the pinion is coated in oil and placed in a polishing machine which utilizes small nut shell particles to polish all surfaces.
Some watch collectors have no doubt read about certifications which are awarded in the form of a “seal”, such as the Geneva Seal (in French, the “poinçon de Genève”) based upon meeting certain criteria. One of the criteria requires work be performed in Geneva; since the Vallée de Joux is located in the Canton de Vaud, no marque such as Blancpain which is located there is eligible. Nonetheless it is often asserted in Geneva that the hand polishing of pinions required for the Geneva Seal endows the components with a degree of superior quality. Certainly in comparison with an unfinished pinion that argument carries with it a measure of truth, but when compared to a precision polished pinion such as those utilized by Blancpain the assertion not only is no longer valid, the opposite is true. The carefully controlled polishing with nut material which is used for Blancpain pinions produces a refined sheen that to the eye is indistinguishable from hand polishing. But that is not the reason Blancpain has chosen the alternative method. The reason is the precision of the finished component. Inevitably when a pinion is polished by hand there will be alterations in the dimensions of the teeth and the shaft. Polishing a little too long on one tooth, not quite long enough on another tooth and precision is lost. It is impossible to avoid this degradation with a hand process that depends on operator judgment and feel. On the other hand, Blancpain’s process is tightly controlled and precision in the fabrication of the pinion is fully preserved in the polishing process. Tolerances are on the order of two microns, something that no hand method can come close to achieving. Although not blessed with a “seal,” real value is delivered to the owner of the watch as these far tighter tolerances offer superior performance and less wear for the finished watch.
There is one more important fabrication process, that for mobiles. Mobiles are a combination of a wheel and pinion. As each element is separately made, what remains is uniting them together. This is done in an operation called “rivetage” or riveting. An almost microscopic edge is manufactured on one face of the pinion. When that edge is firmly placed upon the wheel and the right degree of pressure is applied, the two elements bond solidly one to the other.
If there is any single theme that emerges from the study of wheels and pinions it is the quest for precision. That same obsession with precision applies to the riveting of mobiles. The two elements must be carefully placed one upon the other so that they are absolutely concentric, solidly bonded, and perfectly flat.
The stacking of wheels upon a wire prior to the cutting of teeth.
Quality is tightly controlled to meet each of these strict criteria. This includes verification testing, some of which is destructive. Concentricity can be measured to fractions of a micron. Validation of the method of riveting is not done on every component as it is, in fact, de- structive. However to ensure that the appropriate pressures to rivet are applied a sample finished mobile is placed upon a testing machine to measure the force of the bond. In the machine, the wheel is fixed in place and the pinion twisted until they separate. The force is measured to ensure that it meets Blancpain’s specifications.
One of the profound joys of watch collecting, particularly in our age of open case backs, is admiring the exquisite finishing details of haut de gamme mechanical movements. Hopefully with eyes now opened to the complexities and challenges of fabrication of wheels, pinions and mobiles, more collectors will gaze upon these components with same ardor and intensity as with the other finely finished components of the movement.