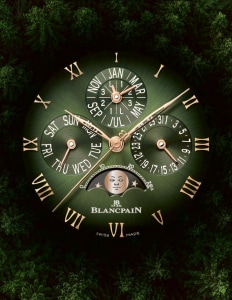
Chapter 6
Its virtues of robustness, versatility, and comfort have earned the NATO strap a prominent place in the Fifty Fathoms collection.
With the name seemingly a dead giveaway, watch aficionados all know that NATO straps have a military origin. Oddly enough, though, not the NATO that is always in the news. That military NATO, the North Atlantic Treaty Organization, cannot lay claim to either the design or the creation of the specification of what we now know as NATO watch straps. Rather, it is the British military that is rightly credited with parentage. At the outset, for the British, the name in actual use was “G-10”, a shortened reference to the British G-1098 form required for personnel to obtain the strap. Why then the name “NATO”? This comes from appending a NATO stock number to the G-10 straps. With over 1 million different military items from NATO member countries placed into a common catalog, of course, reference numbers become essential. So it is that the G-10 was placed into the NATO stock system as 6645-124-2986 (for the army) and 6645- 99-527-7059 (for the air force). Hardly names that slip easily off the tongue, so the parlance became simply “NATO”. Whether you choose to call the strap “NATO” or “G-10”, the strap claims its own storied history.
Commonly, the birth of the NATO strap is pegged at 1973—the year that saw the British publication of Defence Standard 66-15 (dated November 30, 1973) and the debut of form G-1098—but that omits a much longer history that led to those British initiatives. For decades prior, American and European militaries focused attention on the bands for what were then known as “field watches” issued to their troops. Far removed from fashion, the impetus for the design of a field watch strap was intensely practical. Durability, safety, and comfort were the key factors. Air-conditioned office buildings, posh restaurants, driving a luxury automobile, strolling along the Champs- Élysées as a boulevardier, Joint Chiefs of Staff meetings were not the environments front and center in military thinking. Rather, the worries were exposure to arctic cold, desert heat, rain, salt water, perspiration, raw environments, and general rough and tumble on a battlefield. The mandate: “fail-safe in survival scenarios”. Metal bands were considered too uncomfortable in extreme temperatures. Fine alligator or leather insufficiently durable, particularly when exposed to moisture, plus not quick to dry. On the other hand, a solid wraparound strap made of breathable material was seen to offer superior resistance to the elements, rugged use, and a greater range of comfort in a variety of conditions.
A vintage Blancpain Bathyscaphe.
A NATO strap diagram from the 2001 British military specification 66-47.
The aftermath of World War II saw the debut of many efforts to find the ideal material and design. Early on, woven straps were seen as the solution. Woven material became favored for its breathability and drying qualities. To facilitate rapid changing and allow for a wide range of arm widths, including wear on the outside of the uniform sleeve, many were simply a single band threaded through the spring bars. There were plainly disadvantages to this minimalist design. First, the watch could slide back and forth along the length of the strap. Second, and more perilous, if the strap broke, there was nothing retaining the watch itself. Two approaches to these shortcomings soon debuted and, indeed, became common in the 1950s. One was the introduction of loops fixed to the strap straddling either side of the watch head. These would prevent sliding of the watch along the strap. The second was far superior. Instead of loops placed on either side of the watch, there were fixed connections through which the spring bars would be passed. With this system, the strap would flow beneath the watch. If a spring bar failed or if one of the connections broke, the watch would still be retained by the other spring bar connection.
Defence Standard 66-15 can be seen as an evolution of these post-war early attempts to define the ideal watch strap. Military organizations revel in promulgating specifications and standards for essentially everything, and the British were no exception when they issued British Defence Standard 66-15 entitled “Strap, Wrist Watch”, which formally established the design criteria. It specified a cross-woven nylon ribbon as the strap material. Further, the formulation of nylon was to be “free from additives which may act as an irritant to the wrist under extreme conditions”. This addressed several longstanding issues: breathability, moisture resistance, rapid drying, and skin comfort. Nylon was better in all respects than woven cloth. The specified design called for three loops along the length of the strap. This configuration allowed for not only rapid installation on the watch, but also enabled two layers of the strap to pass between the back side of the watch and the wearer’s wrist. The double back-side layering adds to both security and comfort. Further details targeted robustness. Unlike many of the earlier military straps, holes for the tang buckle were required. Previously, many field watch designs were content with simply pushing the tang through the weave of the cloth strap. Additionally, both the holes and the ends of the strap were to be heat-sealed to minimize the risk of fraying.
The Fifty Fathoms Automatique.
Of course, leaving no detail to chance, 66-15 also specified the color, romantically known as “Admiralty Grey”. Less romantically, this color was specified in the document as “BS 4800 card number 3, reference 18B25”. Two changes were to occur with the 2001 update to the specification, numbered 66-47. First, the width was increased from 18 mm to 20 mm. More evocative was the opening of the color palette. Regimental stripes were added to the mix. Doubtful, though, that any soldier would admit to “matchy matchy” with the stripes on his watch band matching the regimental stripes found on his woven double- buckle belt.
With the design now so well evolved and proven, and its virtues of comfort, robustness, and versatility so well established, NATO straps have earned their place in Blancpain’s strap offerings. Blancpain has, however, evolved the genre. It has melded its devotion to environmental protection of the ocean into the production of its NATO straps through the use of nylon recycled from fishing nets.
The first step is essentially an ocean cleanup initiative. It is estimated that each year, 640,000 tons of nylon nets are lost at sea. The toll from this waste is devastating: countless numbers of marine animals become entangled, leading to suffering and loss of life. Locating and removing these polluting nylon nets from the ocean is rightly seen as a double win. It both removes a biohazard from the environment and reduces the need to manufacture new nylon.
What follows to convert this salvage into useable nylon filaments is complex. After cleaning and safely disposing of nylon that is not suitable for reuse, the nets undergo chemical depolymerization producing pure uncolored granules. This now perfect raw material can be colored, transformed into threads and, thereupon, woven into strap material.
A wide range of NATO strap options are available for both the Fifty Fathoms and the Bathyscaphe.
Recycled materials in general play an important role in environmental protection. Blancpain’s straps made using recycled fishing nets, however, go one step beyond commonly seen recycled products, producing a double environmental benefit. The recycling of the nylon carries with it the conventional virtues of reuse. There is a second bonus, however. Since the nets are themselves a form of pollution, their removal from the ocean actually cleanses the environment. Thus, Blancpain’s purchase of this recycled nylon helps fund ocean cleanup.
Many NATO straps found on the market are constructed with metallic loops. Unfortunately, these metallic elements do not offer the same level of comfort as the rest of the strap fashioned in nylon. The solution is obvious. Replace the metal loops with ones constructed of nylon.
Blancpain offers NATO straps in a broad array of colors for all of the models found in the Fifty Fathoms collection.
A Bathyscaphe Chronographe fitted with the optional NATO strap.