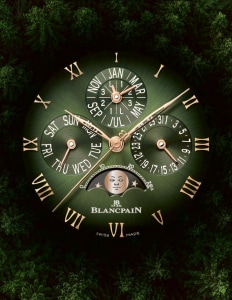
Chapitre 5
Introduction de la céramique haute technologie dans le monde de l’horlogerie.
L’innovation en horlogerie suit une trajectoire longue de plusieurs siècles, qui n’a pratiquement jamais cessé d’aller vers le haut. Bien que cette trajectoire soit ascendante, elle a connu des variations de cadence qui n’ont pas toujours concerné les mêmes éléments. Certaines époques ont été marquées par l’invention de nouveaux concepts mécaniques, d’autres par le développement des métiers d’art, d’autres encore ont donné la priorité à l’esthétique. Pourtant, on retrouve toujours la même constante : les matériaux. Les innovations dans ce domaine ont suscité des avancées sur le plan de la chronométrie (spiraux, balanciers, pierres, roues), de la robustesse (rubis, glace de la montre) et même de l’art (nouveaux ingrédients).
Les complications et constructions prestigieuses d’aujourd’hui sont en réalité le ref let des designs imaginés pour les montres de poche il y a deux siècles. Dès lors, les nouveaux matériaux, qui ont toujours été au centre des avancées du monde horloger, jouent un rôle immense dans la phase d’innovation. L’attachement de Blancpain à l’innovation l’a conduite à intégrer dans ses garde-temps ce qui se fait de mieux en matière de technologie des matériaux : spiraux en silicium, membranes en métal amorphe, roues réalisées selon la technologie LiGA, alliages haute performance pour les ressorts, alliages de titane spéciaux pour les balanciers, les boîtiers et les bracelets, boîtiers en or bronze – pour n’en citer que quelques-uns. Dans cette liste, la céramique occupe une place de choix pour la fabrication des boîtiers, des lunettes et désormais des bracelets.
L’intérêt grandissant du monde de l’horlogerie pour la céramique ne doit rien au hasard. Si l’on devait dresser la liste des qualités prisées pour les boîtiers et bracelets de montres, y figureraient à coup sûr la durabilité, la résistance aux rayures, la légèreté, les propriétés hypoallergéniques et le vaste choix de couleurs. La céramique ne se contente pas de cocher toutes ces cases : elle surpasse tous les autres matériaux. Prenons par exemple la durabilité et la résistance aux rayures. La mesure standard est celle de la dureté, exprimée sur l’échelle de Vickers. La dureté de l’acier inoxydable conventionnel atteint 250 Vickers ; celle de l’or, 100 Vickers ; et celle du titane grade 23, 300 Vickers. Avec 1200 Vickers, la céramique les bat à plates coutures.
Voici une anecdote qui permet de se rendre compte de ce que cela représente. J’ai un jour posé ma Bathyscaphe en céramique sur mon bureau pour vaquer à mes occupations, laissant mon berger allemand de 40 kilos seul dans la pièce. À mon retour, j’ai retrouvé les vestiges de mon bracelet en toile de voile – pourtant solide – éparpillés sur le sol et parmi eux, ma montre, laquelle avait manifestement fait les frais de la frénésie de mon chien. À ma plus grande joie, mais sans surprise pour un spécialiste en science des matériaux, un examen de la montre sous la loupe experte d’un horloger a révélé qu’elle n’avait subi absolument aucune rayure. Les 1200 Vickers ont résisté sans difficulté aux crocs d’un berger allemand. Score final : boîtier en céramique 1, chien 0.
Bathyscaphe Quantième Complet Phases de Lune
La céramique l’emporte encore haut la main face à ses « concurrents » en termes de légèreté : elle est presque 70 % plus légère que l’or, et 25 % plus légère que l’acier.1 Certes, l’or offre un éventail de couleurs variées : jaune, nuances de rose/ rouge, et blanc. Mais les possibilités permises par la céramique sont pratiquement infinies. Aujourd’hui, la collection de Blancpain propose du gris plasma, du noir, du bleu, du blanc et du vert.
Avec de telles qualités, comment expliquer que la céramique ne soit pas plus largement adoptée par l’industrie horlogère ? La réponse est simple : réaliser des boîtiers et bracelets en céramique est démesurément complexe et terriblement exigeant en termes de détails et de finitions à la main. Rares sont ceux qui maîtrisent le savoir-faire nécessaire à la production des composants, et plus rares encore ceux qui répondent aux normes strictes de la HauteHorlogerie. Une visite de la manufacture céramique du Locle, située à seulement quelques mètres de la frontière entre la France et la Suisse, démontre toute la maîtrise de la science des matériaux et l’expertise artisanale requises pour créer les garde-temps en céramique de Blancpain.
À bien des égards, parler de « boîtiers » et de « bracelets » en céramique est réducteur. Prenons par exemple le « boîtier » de la Bathyscaphe Chronographe de Blancpain. La céramique n’est pas seulement utilisée pour la carrure, elle l’est aussi pour la lunette, le fond de boîtier, les poussoirs et la couronne. Idem pour la boucle du bracelet. Sur les versions récentes avec bracelet en céramique, seule la fermeture est en titane. Chacun de ces éléments requiert la mise en œuvre de différents procédés. La carrure, la lunette et le fond de boîtier sont réalisés par pressage. La fabrication des autres composants, comme la couronne, les poussoirs et les maillons du bracelet, se fait par injection. Malgré leurs différences, ces deux procédés ont un point commun : la complexité vertigineuse de leurs détails et finitions main.
1 La céramique pèse environ 6 g/cm3, l’or 19,3 g/cm3 et l’acier inoxydable, 8,03 g/cm3.
Bien qu’il s’agisse de deux procédés distincts, tous deux utilisent de la poudre d’oxyde de zirconium (ZrO2). Sa couleur blanche nécessite dans les deux cas une deuxième étape pour obtenir le spectre de couleurs proposé dans la collection Blancpain – noir, gris plasma, bleu, vert... –, consistant à mélanger la poudre de zirconium avec au moins un pigment high-tech. Cette étape peut sembler anodine, mais elle implique en réalité une myriade de paramètres et requiert une préparation et une précision importantes pour obtenir la teinte voulue. Outre le ratio pigment/poudre, qui doit être strictement défini, le choix du matériau utilisé pour les pigments relève d’une expertise rare en science des matériaux. Compte tenu de la cuisson haute température qui intervient plus tard dans le processus, il faut prendre en considération l’impact de la chaleur sur la couleur. Par exemple, le pigment utilisé pour la céramique noire est gris ou brun avant d’être chauffé. La sélection des pigments high-tech utilisés nécessite donc un mélange d’ingrédients dont la couleur se révélera lors du frittage, un procédé de chauffe sur lequel nous reviendrons bientôt. Une ingénierie minutieuse est nécessaire pour parfaire l’étape de pigmentation et ainsi obtenir la teinte désirée de manière prévisible et durable.
La pigmentation se conclut par le broyage humide de la poudre et du pigment afin de garantir leur homogénéité, l’objectif étant d’enrober de pigment chaque grain de poudre.
C’est à cette étape que le pressage et l’injection empruntent des chemins diffé- rents. Pour le pressage, différents liants sont ajoutés pour obtenir une poudre humide. Le mélange est ensuite transformé en poudre sèche à l’aide d’un procédé de pulvérisation et séchage par atomisation. Une quantité précise de poudre ainsi préparée est alors déposée dans un outil et compactée à haute pression. Interviennent là encore des paramètres complexes : le degré de pression (plusieurs tonnes !), le nombre de cycles dans l’outil, et bien d’autres. Même la géométrie de l’outil résulte d’une étude minutieuse, car l’étape qui suit le pressage, appelée « frittage », va entraîner une perte de dimension. Le frittage consiste à chauffer la poudre à haute température pendant une durée précise, déterminée par la chaleur, la durée et la fréquence des augmentations de température, ainsi que la durée totale du procédé (plusieurs jours). À l’instar de la plupart des composants de Haute Horlogerie, en particulier lorsque l’étanchéité est en jeu, le procédé doit être étroitement contrôlé afin d’obtenir précisément les dimensions finales souhaitées, tout en respectant des tolérances strictes.
La couleur gris plasma requiert un procédé de chauffe supplémentaire. Les composants subissent un traitement à ultra-haute température par plasma, qui transforme l’oxyde de zirconium en carbure de zirconium. Cette transformation crée une teinte grise plasma unique qui ressemble à s’y méprendre à de l’acier inoxydable.
Les composants produits par injection suivent un chemin légèrement différent. Après le « broyage humide » du mélange poudre et pigment high-tech, celui-ci est séché par pulvérisation et atomisé. Différents liants brevetés sont ensuite incorporés à la poudre colorée, le tout dans un environnement contrôlé. Ce mélange est alors écrasé et granulé à la bonne taille, laquelle lui permettra ensuite d’être injecté.
Les moules eux-mêmes demandent un important travail d’ingénierie. La géométrie doit ainsi tenir compte de la perte de dimension qui interviendra plus tard, mais également de la structure et de la position du point d’injection. L’injection génère en effet un résidu, poétiquement appelé « carotte », qui doit pouvoir être retiré facilement. Après l’injection, une partie des liants est éliminée chimiquement, ce qui laisse des pores microscopiques dans le composant en céramique. Le frittage, là encore réalisé selon des températures et des durées précises, permet d’éliminer tous les liants résiduels et de réduire le composant pour lui donner la taille et la forme pré-finition voulues.
À ce stade, les composants réalisés par pressage et par injection sont loin d’être achevés. Avant d’être finalisés, ils doivent encore faire l’objet d’un travail de haute précision reposant à la fois sur des technologies modernes et sur des finitions main détaillées.
Donner au boîtier sa forme finale demande une quantité de travail considérable. Autour du poignet ou au creux de la main, le boîtier dévoile uniquement ses lignes extérieures. Les éléments intérieurs qui abritent la lunette, le mouvement et le fond de boîtier demeurent invisibles. Des heures de meulage sont nécessaires pour façonner ces pièces essentielles. Le fini satiné s’inscrit dans l’ADN esthétique de la Bathyscaphe. Un examen attentif de la montre révèle toute la complexité et la sophistication de ce procédé. La carrure est ornée de fines lignes satinées horizontales ; entre les cornes, elles s’affichent verticalement.
Deux chiffres permettent d’illustrer la complexité des finitions réalisées à la main. Prenons la boucle en céramique des Bathyscaphes munies d’un bracelet en tissu. La boucle seule compte plus de 40 facettes différentes, que les artisans en charge des finitions doivent travailler une par une, facette par facette, en repassant souvent plusieurs fois sur chacune d’elles. Le boîtier en compte encore davantage : plus de 50 facettes, chacune nécessitant un travail de finition individuel.
Ce type d’innovations et de détails sont légion dans le nouveau bracelet en céramique de la Bathyscaphe – le procédé a d’ailleurs produit deux brevets. Chaque maillon du bracelet est réalisé par injection. Les segments sont initialement munis d’une patte permettant d’exécuter l’usinage qui suit le procédé d’injection. Chaque maillon est ensuite fini à la main, ce qui leur confère cette texture satinée. Créer un bracelet de Haute Horlogerie est une tâche particulièrement exigeante. Si l’ajustement des éléments est trop lâche, le bracelet sera mal ajusté ; s’ils sont trop serrés, il y a un risque de blocage. Les tolérances sont de ce fait étroites. Les maillons sont donc soigneusement mesurés, vérifiés et corrigés un par un pour garantir un ajustement parfait. Quel que soit le matériau utilisé pour le bracelet – métal ou céramique – les maillons sont reliés à l’aide de goupilles métalliques. La plupart des montres possèdent des goupilles rondes. Pour la Bathyscaphe en céramique, Blancpain a opté pour une construction plus sophistiquée. Les goupilles ont ici une forme de came brevetée qui permet d’assurer la flexibilité du bracelet fini.
Les lunettes en céramique de Blancpain soulèvent leurs propres défis. Prenons par exemple la lunette de la 70th Anniversary Act 3. Elle arbore un large index triangulaire à 12 heures, des chiffres arabes à 3, 6 et 9 heures ainsi que des index bâtons toutes les 5 minutes. Bien que les creux ménagés pour les index soient découpés au laser, ils sont remplis à la main. Cela s’avère particulièrement difficile pour le grand triangle, car l’application du matériau doit être uniforme sur une surface relativement large. Le Super-LumiNova utilisé pour les index est donc appliqué à la main à l’aide d’un microscope binoculaire permettant de garantir l’uniformité. De même, les index ornant la lunette de la Bathyscaphe Chronographe sont réalisés à la main. Bien que l’artisan puisse s’appuyer sur un outil spécialement conçu pour doser avec précision la quantité de matériau nécessaire, les ajustements finaux sont laissés à son appréciation experte. Il saura par exemple que le chiffre « 1 » nécessite moins de matière que le chiffre « 4 ».
Même si les boîtiers et autres composants en céramique de la Bathyscaphe peuvent résister aux attaques d’un berger allemand, ce sont évidemment les autres qualités de ce matériau qui ont joué un rôle central dans le processus de développement de Blancpain : sa dureté, sa résistance aux rayures, sa légèreté, son confort et la large palette de couleurs qu’elle offre.