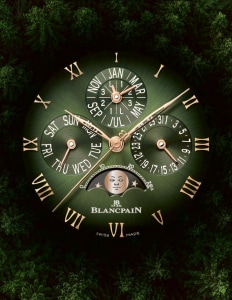
Chapter 6
The material of choice to combine high strength, light weight, corrosion-resistance, and wearability.
The first rule from Blancpain Habillage (Blancpain’s case making workshop1) for taming titanium while machining: Be patient and gentle. Violate the rule and, notwithstanding its strength and durability, titanium during machining, in a fraction of a second, may explosively burst into flame.
Noting the fickleness of the gods of Greek mythology and the challenges that arise in machining, it is fitting that one of the two discoverers of titanium (yes, two are credited with the discovery) named the metal after the Titan gods. Actually, German chemist Martin Heinrich Klaproth, who gave his discovery the name “titanium”, did so not because of its strength and durability, which were not then well known, but because of its stability2. The other discoverer, operating independently and seemingly before Klaproth, William Gregor, made his finding in Cornwall, England in 1791. Both a clergyman and amateur mineralogist, Gregor appended the name “menchanite”. He may have been first, but Klaproth’s name carried the day.
It is remarkable that titanium is only a relatively recent arrival to the world of watchmaking. After all, it is the ninth most abundant element in the earth’s crust and is found essentially everywhere. Not only is it found in nearly all living things, we ingest on average 0.8 milligrams of it per day! Notwithstanding its omnipresence, it took nearly a century and a half following its discovery for there to be a commercially viable process to extract its ore. That did not occur until 1930. It was longer still until methods were developed to work with it.
The properties of titanium have provided a powerful impetus for mastering the difficulties in extracting and machining it. Its strength to density ratio is the highest of any metal, being stronger than low carbon steel but 45% lighter. In addition, it offers extra-ordinary resistance to corrosion, including resistance to salt water, while at the same time maintaining its silver color. Finally, important for applications touching skin, it is non-allergenic. Seen holistically, it truly is the material of choice for those who want to com- bine high strength, low weight, corrosion-resistance, toughness, and wearability. In short, a menu of properties ideal for sport watches.
1 Blancpain cases and bracelets are produced in-house in the Blancpain workshops located in Delémont in the north of Switzerland near Basel. This Blancpain workshop is known internally as Blancpain Habillage.
2 A somewhat anomalous reference in that, according to mythology, the twelve Titan gods, their father and their progeny were anything but stable, leaving a trail of plots, schemes, and wars.
A succession of production stages of Bathyscaphe case bodies.
Notwithstanding the compelling reasons for fashioning watch cases and bracelets in titanium, that is to say use on the exterior, Blancpain’s first application of titanium was on the interior as a movement component. When the first of its new generations of movements debuted in 2006—the caliber 13R0 8-day power reserve manual winding movement—titanium was selected for the balance wheel. Its light weight reduced the consumption of energy, contributing to the achievement of a long power reserve.
Of course, the second step, titanium cases and bracelets, is now here. However, there is much more to offering titanium watches than simply fashioning the elements in pure titanium. Indeed, pure titanium is far from ideal for use in timepieces. Instead, its properties are enhanced with the addition of a small amount of aluminum (6%) and a small amount of vanadium (4%)3. This alloy is commonly referred to as Grade 5. Some refer to Grade 5 as “medical grade”, as it is the best for such medical applications as joint replacements. Placed above Grade 5 is a variant known as Grade 23 or Extra Low Inclusions (“ELI”). The difference is purity, with Grade 23 being of a higher degree as it has a reduced percentage of oxygen. To qualify as Grade 23, the maximum percentage of oxygen cannot exceed 0.13%. Reducing the amount of oxygen improves the fracture toughness of the metal. It becomes the top choice for its superior strength, light weight, corrosion-resistance, and toughness. It is this improved performance that led Blancpain to select Grade 23 for six recent models with titanium cases. All six hail from the sport collection: two versions of the Air Command chronograph (in two different sizes, one 42.5 mm in diameter, the second 36 mm), three Bathyscaphe models (the complete calendar moon phase, the chronograph, and the automatique), and the Fifty Fathoms Tourbillon. All of the titanium Bathyscaphe versions offer the option of a titanium bracelet.
For all of its virtues, titanium exacts its price when it comes time to produce a watch case or bracelet. The hardness and toughness that make it so desirable in the final product make it vastly more difficult to machine and polish than steel or gold. Although Blancpain produces its titanium cases in the same case/bracelet facility as its other metals, the processes and even the machines used for titanium are different. The process begins with stamping at a high temperature the rough form of the case body with its lugs from a sheet of titanium, whose thickness is determined by the final thickness of the case body. The process differs greatly from the beginning steps employed for a steel or gold case. For those, the time-honored methods of stamping at cold temperatures are followed. The details of high-temperature stamping are closely guarded industrial secrets. The parameters are exacting: temperatures, atmosphere, cooling times, the stamping tool all play important roles. Broadly speaking, the sheet is treated multiple times. After each heating in a specified atmosphere, the metal is allowed to cool. Metallurgists refer to this technique as annealing, which conditions the material. The end product of these steps is a rough form of the case and its integrated lugs.
3 Vanadium, like titanium, is a transition metal. “Transition” refers to its position on the periodic table of elements, in the top of the row joining the two columns on the sides. Vanadium is widely present in nature. It is found in microscopic quantities in such diverse items as black pepper, shellfish, parsley, and grains.
Separate processes are followed for the titanium case back and bezel. With these processes, the components are machined from a long bar of titanium. However, the requirements of heating and cooling remain in order to ensure the quality of the machining. Omitting annealing risks deformation.
What follows at Blancpain Habillage is no less demanding of savoir faire than the cutting/annealing process. For the case body itself, the first stage of machining is termed tournage (circular carving). A rotating cutting tip, which can be thought of as a type of “chisel” (termed a “burin à plaquette”), whose form is dictated by the particular case element being carved, is pressed upon the case, which is at the same time turned in the tool. In its broad outlines, this resembles a core case machining method dating from more than a hundred years ago. This first step fabricates the inner diameter of the case body, which for the subsequent steps also serves as a reference point. Likewise, it resembles the tournage process for a steel or gold case body. However, titanium imposes its own set of unique requirements. First is cooling of the cutting tool. With other materials, an oil slurry is used. That would not be advisable with titanium because of the high heat generated by the cutting tool. Instead, a water-based emulsion is used. Nonetheless, the risk of flame and explosion remains. Therefore, the tools dedicated to machining titanium are all equipped with high-performance flame detection and extinguishing safety systems. In but a fraction of a second, these systems can spring into action to prevent a conflagration.
There are multiple machining steps dictated by the details of the case design, each step targeting a particular element of the case body and each demanding a uniquely shaped cutting tip. Extremely close tolerances must be respected for each step. This is true for every Blancpain, but becomes even more critically important to achieve the high degree of water-resistance required for diving watches such as the Fifty Fathoms and Bathyscaphe. High precision is the order of the day for the proper fitting of case backs, bezels, and seals.
Other operations await. One important step is the drilling of holes, which must be done for the crown and—for the attachment of straps—the lugs. The Air Command chronograph adds additional holes for the two chronograph pushers. The drilling, termed “réalisation des logements par fraisage” (creating the housing by drilling) demands a similar degree of precision as tournage. The same precautions and spe- cial measures against sudden flame and/or explosions are required.
Following the completion of these multiple stages of tournage and fraisage are the handcrafts of fine finishing, engraving, and polishing. One example of the handwork is the use of classic milling stones to create perfect crisp junctions between the lugs and the case body. These are double-sided tasks, as there are borders on both the outside and the inside of the lugs. Not only must the junctions be stone milled with crisp lines, but care must be taken to maintain the flat, straight profile of the inside surface of the lugs. This finishing tool itself recalls tradition, as it consists of a rotating abrasive stone. For the craftsman to achieve a sharp bright joint between the lugs and the curved side of the case is particularly painstaking and time-consuming. Once the careful milling of the junction between the case and lugs has been completed, several additional artisanally applied machining steps follow. Polishing comes next, which has to be meticulously performed by hand in order to avoid disturbing the precisely formed line between the lugs and the case body.
Finishing has always been the province of highly skilled specialists, particularly so with complex shapes and texture combinations. The titanium Fifty Fathoms models have brushed finishes on all of the case surfaces. The challenge for the finishing craftsmen is to ensure that the fine lines of the brushed surfaces are consistent both with respect to the degree of brushing and with respect to the direction of the subtle lines. Extra deftness is called upon in the area where the lugs join the case. The brushing cannot touch or disturb the crisp bright junction that was milled earlier.
The two versions of the new titanium Air Commands present another test of skill. The top surface of the lugs features both a brightly polished segment and one that is brushed. The border between the two must remain precisely defined and perfectly positioned. This can only be accomplished by placing plastic protection on one of the zones while finishing the other.
Polishing the flanks of a Fifty Fathoms case is a demanding operation requiring great precision and handwork in order to achieve a crisp junction between the lugs and case body.
A catalog of additional steps are invoked for the rotating bezels and the case backs. A rotating bezel is an essential feature of both diving and aviation timepieces. To facilitate turning the bezel, some form of knurling to aid gripping is part of the design and must be formed on the exterior. As all of the bezels feature an insert with the bezel markings—ceramic in the case of the Bathyscaphe and Air Commands, bombé sapphire crystal for the Fifty Fathoms Tourbillon—this necessitates creating a groove in which the insert will be nestled. Tournage is the method used to form the groove. The tolerances for this machining are extraordinarily precise, as the fit between the ceramic or sapphire insert and the metal groove must be perfect. Finally, the diving watch bezels include very fine, precisely placed small teeth on the underside of the bezel, which form a part of the unidirectional rotating system. Those teeth are stamped into the bezel.
Debuting alongside these new models are titanium bracelets for the three Bathyscaphes and the Fifty Fathoms Tourbillon. On the one hand, the bracelets are new in that they are the first Grade 23 titanium bracelets for the Fifty and Bathyscaphe. On the other hand, the style is emblematic for Blancpain dating back to the ‘90s. Connoisseurs will at once recognize the signatures of the classic Blancpain 71 steel bracelets, renowned for both their elegance and comfortable fit upon the wrist.
A Fifty Fathoms case body.