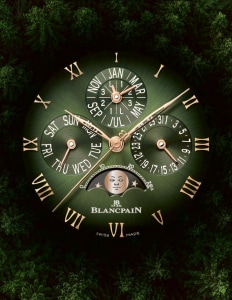
Chapter 11
Although seldom heralded by the public, specialized custom tools are watchmaking essentials.
What is the ultimate solution for life removed from the public eye? Enrollment into a witness protection program and being whisked off under a new name? Lodging in a CIA or MI6 safe house in a remote forest? Both effective but, admittedly, a bit extreme. What about becoming a watchmaking tool designer and fabricator? Not the generic tools, such as screwdrivers, fine tweezers, dust coverings, and the myriad of other watchmaking tools sold by Bergeron and other specialty suppliers. Rather custom tools, specifically conceived to aid watchmakers in the assembly and finishing of particular calibers. These are all done in-house, are never sold on the market, but are essential for movement production. However vital these custom tools may be and no matter how dependent watchmakers are upon them, never are the creators celebrated by watch aficionados, featured on Instagram, or awarded GPHG prizes. They are accorded anonymity approaching that of safe-house residents.
On the other hand, if you are fortunate enough to visit Blancpain’s two workshops in the Vallée de Joux (the larger in Le Sentier, the second one 3 km away in Le Brassus) and if you are a keen observer of the watchmakers at work, you will find these custom-designed tools in abundance. Witnessing these tools being used at nearly every stage of the realization of a fine movement provokes two questions: why has so little been said about these enormously clever tool designers and how do they go about practicing their profession? Dear readers, we shall go about exploring the world of the conception and use of these special watchmaking tools, which will both pay homage to their creators and bring to light many dimensions of the métier.
At Blancpain, almost all the highly specialized tools are the product of collaboration between the movement designers (the French term is “constructors”) and the tool designers. These two groups work together to develop the assembly methods for each new movement. As the methods for each stage become defined, both the need to have particular custom tools and the designs of the tools emerge.
One particular tool makes the point of how movement design and tool design come together in an assembly method. Blancpain’s movements utilize free sprung balances. With this design, both ends of the balance wheel’s hairspring are fixed firmly into position.1
1 With a free sprung architecture, the regulation of the watch, i.e. its running rate, is set by adjusting four regulating screws, which are attached to the balance wheel. When they are turned outward, the rate is slowed. Turning them inward does the opposite. Think of an ice skater spinning. When arms are held outward, the spin is slow. As the arms are moved inward, the spin becomes more rapid. This is in contrast to less expensive “raquette” regulation systems. With a raquette, the outside end of the hairspring passes through two pins attached to a movable arm. The watchmaker is able to manipulate the position of the raquette which changes the effective length of the spring. This approach is less resistant to shocks, as the arm may move in response to a shock. As well, regulation is less predictable since the watchmaker has to push the raquette back and forth an indeterminate distance to change the rate.
Blancpain’s in-house developed tool for securing the end of the hairspring to the piton.
Blancpain’s tool designers were called upon to develop a tool that would aid the watchmaker in fixing the far end of the delicate hairspring into a retainer called a “piton”. The tool holds the balance bridge in position so that the watchmaker, aided by a microscope, can place the fine hairspring end into a miniscule slot on the piton, place a grain of solid glue into the slot using tweezers, and manipulate a fine heating element to touch the piton, melting the glue and thus guaranteeing perfect attachment. The design of the tool had to take account of the geometry of each of the components: the balance bridge, the location of the piton, the outer end of the hairspring. Thus, the tool configuration is different according to the specifics of each caliber. For example, the tool for the caliber 1150 with its single balance bridge is not the same as the one for the caliber F385, which has a double-ended balance bridge.
There is one important perspective not to be overlooked in the discussion of not only this hairspring attachment tool but tools in general. The tool may aid the watchmaker in performing the task, but it does not obviate the requirement of enormous skill. In the example of the hairspring attachment tool, several months’ training occurs before the watchmaker becomes qualified.
Remaining on the subject of the balance wheel, Blancpain has created a special tool for the adjustment of the regulation screws. Unlike the attachment of the far end of the hairspring, which is done before the balance wheel, its hairspring and its bridge are placed into the movement, regulation is performed with the balance wheel fully mounted into place. Keeping in mind the contrast between raquette regulation, where the watchmaker moves an arm back and forth observing the timing results (necessarily a rather imprecise method), Blancpain’s inertial regulation is accomplished by turning the balance screws inward or outward. The movement designers (termed “constructors”) are able precisely to specify the changes in rate that will occur based on the number of degrees of rotation of the screws, i.e. a quarter turn will change the rate a specified number of seconds per day. How, then, can the watchmaker not only access the small regulation screws, but also measure the number of degrees that each is rotated? The task sounds rather simple but would be maddeningly difficult without a custom tool. The tool designers answered the call with a perfect solution. They devised an arm whose tip mates with the square head of a regulation screw. The number of degrees of rotation is shown on a marked transparent barrel. As the watchmaker turns the arm, a bar attached to the arm shows the number of degrees on the transparent barrel. As is the case with many clever inventions, this is a solution that once seen seems trivially simple, but which required inspiration to be created in the first place.
The custom tool used to adjust precisely the inertial regulation screws of the balance wheel.
Fine adjustment of the hour disk for the Villeret Tourbillon Heure Sautante.
One of the tasks core to watchmaking is verifying that elements of the movement are assembled properly and functioning correctly before proceeding to next steps. Specialized tools are called upon for these undertakings. Three examples. Following the initial assembly of the balance wheel, hairspring, escapement, and carriage of a tourbillon, the watchmaker places those elements into a custom tool to verify the engagement of the pallet jewel with the escapement. The goal is to attain a minimum, but still sufficient, degree of depth. Too much depth of engagement consumes excess energy and lowers the power reserve. The carriage is fixed upon a mounting and energy is applied to the escapement via a single wheel engaged with the pinion and powered by a small spring. Although the spring is only able to activate the escapement for very brief periods, that is enough for the watchmaker to observe and control the engagement depth of the jewel. This vital controlling step would be essentially impossible with the assembly mounted into the movement. Similar tolerance controls take place during the assembly of the Villeret Tourbillon Volant Heure Sautante Minute Rétrograde. The disk carrying the hour markings is constructed as an assembly that, when viewed in cross section, appears as a sandwich: an hour disk above, then a bridge, then a special wheel below (you saw this coming: with twelve teeth, one for each hour) engaged with other parts of the mechanism that control its changes. It is important to ensure proper turning of the disk, so that it is free to move, but without too much play. That tolerance is exacting and verified by placing the assembly upon a holder custom made for the disk, bridge and wheel and very precisely measuring the depths of the components. Similarly close tolerances are demanded in the construction of the complex Villeret Chinese calendar. For this movement, special tools were created to control the force of finger springs used in the calendar mechanism. Unique holders were created both to control the form of each of the springs and to validate that its tension is correct before it is placed into the movement.
An array of unique movement and component holders for various operations.
The special tool used to control the force of finger springs.
Blancpain’s in-house tool used for adjusting and verifying the depth of the pallet jewels’ engagement with the escapement of the carrousel.
Not all tools call upon the designer to create clever new systems such as the ones described above. That does not mean, however, that the tool—however seemingly pedestrian—is not essential. Consider a minute repeater such as the Carrousel Répétition Minutes. In order for the watchmaker to evaluate the functioning of the repeater and its sound at various stages of its construction, a holder is required. Blancpain’s tool makers fabricated a holder for the movement, of course precisely measured to the caliber, including a slide to activate the sonnerie and an attachment for the sounding rings. The same idea lies behind the holder for the Carrousel Répétition Minutes Chronographe Flyback. This holder allows for activation of the chronograph functions via incorporated pushers.
Some of the tools are built around a commercially available device that has been augmented and adapted by Blancpain for its watchmakers. Blancpain’s movement designers have specified the precise tightness for the attachment of hands. The parameters are specific to each particular hand, with different degrees of tightness for an hour hand, for example, than for a chronograph seconds hand. To meet the design specifications, Blancpain’s tool designers have built an array of pushers for hand attachment, colored differently according to the hand with appropriate strength springs, again defined by each particular hand. Placing the movement unto a pressure-sensing platform, the watchmaker is able to select the correct pusher for a given hand and validate the force on a computer screen. Although the pressure-sensing platform is built externally, the remainder of the tool was devel- oped in-house.
A carrousel minute repeater movement placed into a custom-designed holder.
Tips used for mounting hands.
Finishing of movement components opens the doors to another rich category of special tools. To appreciate the breadth of the tools, consider that there are a whole host of categories of finishes found in a Blancpain movement: for example, fine polishing of edges (“anglage”), circular swirls (“perlage”), Geneva stripes (“côtes de genève”), straight lining of steel components (“traits”), mirror polishing (“poli miroir”) and chamfering (“moulurage”). Then consider that more than one type of finish will be applied to a single component, such as a côtes de genève finish to the flat surface of a bridge, anglage to the edges, and moulurage to the exterior of wells for screws and jewels. Then add to the mix the fact that there are a myriad of different shapes for the components in any given movement, which call upon a specific tool to hold the component for the particular finish being applied. This leads to a dizzying matrix of different tools for each movement. The term “matrix” is a perfect description. Opening one of the drawers of a finishing specialist in Le Brassus revealed an array of holders more than 20 columns wide and 20 rows deep. That equals 400 different special tools, each adapted to the shape of a distinct component for a specific finish.
Blancpain’s tool and holder used for côtes de genève finishing.
The matrix of tools used for different finishing steps of individual movement parts.
Walking through Blancpain’s workshops in Le Sentier and Le Brassus and observing the use of the tools we have described and many others of similar importance, it is remarkable that so little has been said on the internet, on social media or in print publications about this extraordinary watchmaking craft. There is one group, however, that deeply understands the contribution of tool makers: the watchmakers who depend upon their creations.
The specialized holder for finishing the upper bridge of a tourbillon carriage.