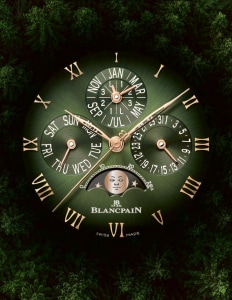
Chapter 5
Bringing high technology ceramic to watchmaking.
The several centuries-long arc of innovation in watchmaking has almost always been upward. Upward it may have been, but not continuously at the same slope and not constantly centered upon the same elements. Some epochs have been marked by new mechanical designs. Others by artistic crafts. Still others focused on aesthetics. Yet running through nearly all of them has been one constant: materials. Innovations in materials have fueled advances in chronometry (hair spring materials, balance wheels, jewels, wheels), robustness (rubies, the watch crystal), even art (new craft ingredients).
Today, where revered complications and constructions reflect designs pioneered in pocket watches as much as two centuries ago, new materials, which have always been front and center in the upward march of watchmaking, now play an outsized role on the innovation stage. Blancpain’s devotion to invention has led it to the forefront of weaving new material technology into its timepiece designs. To name a few: silicon hairsprings; liquid metal membranes; LiGA wheels; high performance mainspring alloys; a variety of special titanium alloys for balance wheels, cases, and bracelets; bronze gold cases; and much more. Occupying a prominent place on that list is ceramic for cases, bezels and now bracelets.
There is a reason for today’s embrace of ceramic in watchmaking. If you were to put pen to paper for a list of prized attributes for watch cases and bracelets, it is certain that list would enumerate durability, scratch resistance, lightness, hypoallergenic properties, and a wide choice of colors. Not only does ceramic tick all those boxes, no other case/bracelet material stays step-for-step alongside it. Consider durability and scratch resistance. The standard measure would be hardness expressed on the Vickers scale. Conventional stainless steel achieves a hardness of 250 Vickers; gold, 100 Vickers; Grade 23 titanium, 300 Vickers. Zirconium dioxide ceramic tops them all at 1200 Vickers.
To put 1200 Vickers into perspective, a real-life story. Yours truly, in order to tend to other matters, left my ceramic Bathyscaphe on my office desk placing my 90 lb. German Shepherd dog in charge of the room. Upon return, I found morsels of the otherwise robust sailcloth strap scattered about, the watch on the floor, plainly having been the subject of a dog’s frolic. To my delight and no surprise to a materials scientist, examined with a watchmaker’s loupe, not even a hint of a scratch or blemish was on the watch itself. 1200 Vickers easily bested the jaws of a large German Shepherd. Final score: ceramic case 1, dog 0.
Bathyscaphe Quantième Complet Phases de Lune
There is a similar triumph for ceramic against its “competitors” when considering lightness. Compared to gold, ceramic is nearly 70% lighter; compared to steel it is 25% lighter1. It is true that gold offers a range of colors: yellow, different shades of rose/red, and white. Ceramic, however, is practically unlimited in its color possibilities. Blancpain’s collection today includes gray plasma, black, blue, white, and green.
So, with its attributes so compelling, why has there not been wider adoption of ceramic by the watch industry? The answer is simple: crafting cases and bracelets in ceramic is toweringly complex, maddeningly difficult in its details, and extraordinarily demanding of finishing hand craft. Only a few have mastered the savoir-faire needed to produce the components, and fewer still to meet the exacting standards of haut de gamme prestige watchmaking. A tour of the ceramic workshop located in Le Locle, mere meters from the Swiss French border, showcases both the material science and hand craft talents that are brought to bear in the creation of Blancpain’s ceramic timepieces.
In many ways labeling the uses of ceramic for “cases” and “bracelets” oversimplifies. Take, for example, Blancpain’s ceramic Bathyscaphe Chronographe “case”. Not only is the body of the case fashioned in ceramic, but the same is true of the bezel, case back, chronograph pushers, and crown. Equipped with a strap, the buckle is ceramic. On the recently introduced version offering a ceramic bracelet, only the closure is in titanium. Different processes are brought to bear for each of these elements. For the case body, bezel, and case back, a pressing process is employed; for the other components such as the crown, chronograph pushers, and bracelet links, an injection process. Notwithstanding the distinctions between the two processes, there is common ground in one respect. Both are staggeringly demanding in their details and hand applied finishes.
1Ceramic weighs approximately 6 g/cm3; gold 19.3 g/cm3; stainless steel 8.03 g/cm3.
Although the two basic processes diverge from each other, both are based upon zirconium dioxide (ZrO2) powder. The zirconium dioxide powder is white in color, so in order to achieve the spectrum of colors found in Blancpain’s collection… black, gray plasma, blue, green…the second step for both processes is mixing the zirconium powder with at least one high tech pigment. Trivial as this may sound, there are a myriad of parameters that come into play and that call for careful study and precision to arrive at the desired hue. Not only is the ratio of pigment to powder tightly defined, but the selection of the pigment material is a matter of well- studied material science expertise. As high temperature baking will occur later in the process, account must be taken of how heat affects the color. An example: the pigment for black ceramic is gray or tan before heating. The selection of high tech pigments requires mixing a range of ingredients whose color will develop during sintering, a heating process which we will turn to momentarily. Careful engineering is called upon to perfect the pigmentation step to arrive at the desired hue both predictably and durably. The pigmentation step concludes with wet grinding of the powder and pigment to ensure proper mixing with the goal of enrobing the individual grains of the powder with pigment.
It is at this point that the pressing and injection processes take different paths. For pressing, multiple binders are added resulting in a wet powder. Thereafter, the mixture is readied in a spray drying atomization process. The prepared powder is deposited in a tool in a precisely measured quantity and pressed at high pressure. Again, the parameters are complex: the degree of pressure (several tons!), cycles in the tool and more. Even the geometry of the tool is the product of careful study, as the step following the compression, called “sintering”, will shrink the size. Sintering means baking at a prescribed high temperature for a time defined precisely by the temperature, the period and rate during which the heat is raised, and the duration (several days in length). In common with essentially all elements of fine timepieces, and particularly so where water resistance is involved, the process must be tightly controlled to produce the precise final dimensions within tight tolerances.
The gray plasma color imposes an additional heating process. Those components undergo an ultra high plasma heat treatment which transforms the zirconium oxide into zirconium carbide. That transformation produces a unique gray plasma color that closely resembles stainless steel.
Injection produced components travel along a slightly different route. After “wet grinding” of the combined powder and high tech pigment, the mixture is spray dried and atomized. In a controlled environment, multiple patented binders are incorporated into the colored powder to complete the mixture. This combination is then crushed and granulated to a prescribed size that facilitates and readies it for injection.
The molds themselves are the product of intense engineering. Of course, the geometry needs to account for the shrinkage that will arrive later, but also the structure and position of the injection point. Since a small remnant of the injection will remain, romantically termed the “carrot”, the position needs to be in a location that facilitates its removal. After injection, the patented binders are chemically partially removed, leaving behind microscopic holes in the ceramic component. Sintering, again with precisely defined temperatures and times, removes any remaining binders and shrinks the component to its designed pre-finishing size and form.
At this stage, both the pressed and injected components are far from completion. What remains is painstaking, precise work making use of both modern technologies and detailed hand finishing to bestow final shapes and finishes.
For the case itself considerable work is required to create the final form. On the wrist or in the hand, the case only reveals its exterior forms. Unseen are the interior elements that house the bezel, movement, and case back. Hours of grinding are involved to fashion these essential elements. Satin finishes are an important aesthetic element that distinguishes the Bathyscaphe. Close examination of the watch shows the complexity and sophistication of the satin finish. The case sides feature fine satin lines oriented horizontally; between the lugs the orientation is vertical.
Two statistics illustrate the complexity of the hand applied finishes. Consider the ceramic buckle for those Bathyscaphes equipped with a strap. The buckle alone has more than 40 distinct facets that must be addressed by the finishing craftsmen, one by one, facet by facet, often several times per facet. The case has even more: in excess of 50 facets, each one requiring separate finishing.
Similar innovation and details abound in the creation of the new Bathyscaphe ceramic bracelet. Indeed, the process has produced two patents. Each one of the brace let links, termed “maillons”, is injected. The segments are initially formed with a tab in order to accomplish the machining that follows the injection process. There following, each link is individually finished by hand to bestow its satin texture. The creation of a fine watchmaking bracelet is demanding. If the fit of the elements is too loose, the bracelet will be sloppy; too tight and there is a risk of binding. Hence, the tolerances are tight. Accordingly, one-by-one, the links are carefully measured, verified, and adjusted to ensure a proper fit. Running across any bracelet to connect the links, whether it be metallic or ceramic, is a metal pin. Generally, for almost all watch bracelets, the shape of the pins is round. For the ceramic Bathyscaphe, Blancpain’s construction is more sophisticated. The bracelet pins have a patented cam-like shape which helps ensure a proper range of flex for the finished bracelet.
Blancpain’s ceramic bezels introduce their own challenges. Take for example, the bezel on the 70th Anniversary Act 3. It boasts a large triangular index at 12 o’clock, nume- rals at 3, 6, and 9 and stick indexes at each 5 minute mark. Although the troughs for the markings are laser cut, filling the troughs is done by hand. Particularly difficult is the large triangle, as the application of material has to be even across its relatively large surface area. Using a binocular microscope to ensure evenness, the Super-LumiNova for the markings is applied by hand. In similar fashion, the bezel markings for the Bathyscaphe Chronographe are done by hand. Although the craftsperson is aided by a specially designed apparatus that can precisely dose quantities of the marking material, it is left to the judgment of the specialist to make minute adjustments. For example, less material is needed for the nume ral “1” than the numeral “4”.
Although it is certain that Blancpain did not have German Shepherd jaws in mind when it developed its ceramic Bathyscaphe cases and other ceramic components, ceramic’s other virtues plainly were front and center in the thinking: hardness, scratch resistance, lightness, wearability on the skin, and a broad color palette.