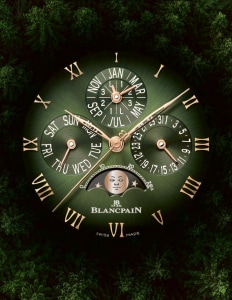
Chapter 5
時計製造にハイテクセラミックを採用。
何世紀にもわたる技術革新により、時計は 常に進化し続けてきました。とはいえ、常に 同じペースで発展してきたわけではなく、進 化の立役者もその時々で異なります。ある時 代には新しい機械設計が革新をもたらし、 別の時代には芸術的な職人技が貢献。審美 性が大きく向上した時代もありました。そう した中、ほぼどの時代にも発展を続けてきた のが、素材です。素材に関するイノベーショ ンは、クロノメトリー(ヒゲゼンマイの素材、 テン輪、宝石、歯車)、堅牢性(ルビー、風防)、 さらには芸術性(装飾に用いられる新たな 材料)の進化を後押ししてきました。
このように、これまでずっと時計の発展の中軸 を担ってきた「新素材」は、200年も前に開発 された懐中時計の設計を範に取った複雑機 構や構造が人々の尊敬を集めている今、イノ ベーションの舞台で極めて重要な役割を果 たしています。常にイノベーションを目指すブ ランパンも、新素材技術を中心に据えたデザ インに取り組んできました。例えば、シリコン 製のヒゲゼンマイ、リキッドメタル製の金属 膜、LiGA加工の歯車、高性能合金を用いた 主ゼンマイ、特殊なチタン合金製のテン輪、ケ ース、ブレスレット、ブロンズゴールド製ケース などです。そのリストの中でも特に重要な素材 となるのが、ケースやベゼル、ブレスレットに用 いられているセラミックです。
今日、時計製造でセラミックが選ばれるのに は、理由があります。腕時計のケースやブレス レットの優れた特徴を書き出してみると、耐久 性、耐傷性、軽量性、低刺激性、豊富なカラー バリエーションなどが挙げられますが、セラミ ックは、そのすべてを満たしているだけでなく、 ケースやブレスレットに使われる他の素材を はるかに凌ぐ性能を持っています。まず注目し たいのが、耐久性と耐傷性。硬さの標準的な 尺度「ビッカーススケール」で表すと、従来の ステンレススティールの硬度は250ビッカー ス、ゴールドが100、グレード23チタンが300 であるのに対し、二酸化ジルコニウム製のセラ ミックは1,200と、他を大きく上回る圧倒的な 硬度を誇ります。
1,200ビッカースがどのくらい頑丈なのかを 説明するために、私の体験談をご紹介しまし ょう。ある日、私は諸用を済ませるために、セラ ミック製バチスカーフを机の上に置いたまま、 短時間オフィスを空けました。留守番をしてい たのは、体重40kgを超える大型犬ジャーマン シェパード。オフィスに戻ってくると、丈夫なは ずのセイルキャンバス製ストラップの切れ端 が散乱し、腕時計は床に転がっていて、明ら かにオモチャ代わりにしてじゃれあった形跡 が……。材料科学者にとっては驚きはないか もしれませんが、時計職人用のルーペでじっ くり調べてみても、時計にはかすり傷一つな く、私はほっと胸を撫で下ろしました。1,200 ビッカースは、大型のジャーマンシェパードの 強靭な顎もなんのその。この勝負は1対0で、 セラミックケースに軍配が上がりました。
バチスカーフ コンプリート カレンダー ムーンフェイズ
同様に、セラミックは「軽量性」においてもライ バルたちを凌ぎます。ゴールドと比べると約70 %、スティールよりも25%軽量です¹。確かにゴ ールドは色合いの豊かさも魅力で、イエロー、 濃淡の異なるローズやレッド、ホワイトなど種 類豊富です。ただ、その点においても負けてい ないのがセラミック。カラーバリエーションの 可能性は実質的に無限大で、ブランパンのコ レクションでは現在、グレープラズマ、ブラック、 ブルー、ホワイト、グリーンで展開しています。 さて、これほど魅力的な特性を持っていなが ら、時計業界でセラミックがそこまで広く採用 されていないのはなぜでしょうか。答えは簡 単。ケースやブレスレットをセラミックで製作 するのは、とてつもなく複雑で、細部の加工は 気が遠くなるほど難しく、仕上げの手作業にも 極めて高い技術が求められるからです。部品 製造のノウハウを習得している職人はほんの ひと握り。「オー・ド・ガム(高級)」と呼ぶにふ さわしいレベルの厳格な基準を満たす職人と なると、その数はさらに少なくなります。フラン スとの国境に近い、スイスのル・ロックル郡に あるセラミック工房を訪れると、ブランパンの セラミック製時計の製造に活かされている材 料科学と手作業による職人技の両方を目に することができます。
セラミックの使用を「ケース」や「ブレスレット」 に分類してしまうのは、あらゆる意味で、単純 化しすぎていると言えるでしょう。ブランパンの セラミック製バチスカーフ クロノグラフの「ケー ス」を例にとってみると、ケース本体だけでな く、ベゼル、ケースバック、クロノグラフプッシャ ー、リュウズにもセラミックが使われています。 ストラップのバックルもセラミック製です。最 近発表されたセラミック製ブレスレットのモデ ルでは、バックル部分のみチタンが用いられて います。これらのパーツの製造工程はそれぞ れ異なり、ケース本体、ベゼル、ケースバックは プレス成形、リュウズ、クロノグラフプッシャー、 ブレスレットのリンク(コマ)などその他のパー ツは、射出成形によって製造されます。これら 2つの成形方法はそれぞれ工程が異なります が、細部の加工と手作業による仕上げに驚く ほど高度な技術が要求されるという点は共通 しています。
1 密度はセラミックが約6 g/cm3、ゴールドは19.3 g/cm3、 ステンレススティールは8.03 g/cm3。
成形法にかかわらず、原料に使用するのは二 酸化ジルコニウム(ZrO2)の粉末です。二酸化 ジルコニウムの粉末は白色で、ブランパンのコ レクションに用いられているブラック、グレー プラズマ、ブルー、グリーンといった色を付け るために、どちらの成形法でも2番目の工程と して、ジルコニウム粉末を少なくとも1種類の ハイテク顔料と混合する作業が行われます。 簡単なことのように思えるかもしれませんが、 顔料の混合には無数のパラメーターが存在 し、希望の色を生み出すには入念な研究と正 確さが求められます。顔料と粉末の比率が厳 密に定義されているのはもちろん、顔料の素 材も材料科学の専門知識を駆使し、十分に 研究を重ねた上で厳選されています。工程の 後半で高温焼成が行われるため、熱によって 色にどのような影響が出るのかについても考 慮しなければなりません。例えば、ブラックの セラミックの顔料の色は、焼成前はグレーま たは褐色です。ハイテク顔料を選ぶ際は、焼 結時(この熱処理工程については、この後ご 紹介します)に発色する様々な原料の配合を 計算しなければなりません。着色の工程に は、予測可能かつ耐久性を備えた希望の色 を実現するために、緻密な技術が求められる のです。この工程で、粉末と顔料を湿式粉砕 し、一粒一粒を顔料でコーティングして均等 に混合していきます。
さて、ここからは、プレス成形と射出成形で実 施される工程が変わってきます。プレス成形で は、複数の結合剤(バインダー)が加えられ、 湿式粉体になった混合材料を噴霧乾燥アト マイズプロセスによって調製。調製された粉 末を正確に計量し、ツール内に充填して高圧 で圧縮します。この工程においても、圧力(数ト ン!)やツール内のサイクルなど複雑なパラメ ーターが用いられ、ツール自体の形状やサイ ズも、圧縮後に行われる「焼結」と呼ばれる工 程での収縮を考慮し、入念な研究に基づいて 製作されています。焼結とは、温度、昇温時間 と速度、期間(数日間)など、正確に定義され たパラメーターを用いて熱を加える工程です。 高級時計の製造では、本質的にすべてのパー ツに言えることですが、特に防水性に関わる パーツの場合、厳しい公差の中で正確な最終 寸法を実現するには、厳密な工程管理が必須 となります。
グレープラズマの色を出すには、追加の加熱 工程が必要で、パーツに超高温プラズマ熱処 理が施されます。そこで酸化ジルコニウムが 炭化ジルコニウムに変化し、ステンレススティ ールのような独特のグレープラズマのカラー が生まれるのです。 一方、射出成形は、これとは少し違った工程 で進められます。複合粉末とハイテク顔料の 「湿式粉砕」の後、混合材料は噴霧乾燥さ れ、霧化されます。管理された環境下で、着色 された粉末に、特許を取得した複数の結合剤 を配合し、混合材料を作成。この混合材料 は、容易な射出とそのための調製に適した大 きさに粉砕され、造粒されます。
ここで使われる金型自体も、徹底した技術の 賜物です。その形状は当然、後に生じる収縮 を考慮したものでなければならず、射出点の 構造や位置も考えなければなりません。 「carrot」という愛称で呼ばれる小さな射出 の跡が残るので、それを除去しやすい位置に する必要があります。射出後、特許取得の結 合剤が化学的処理によって部分的に除去さ れ、セラミック製パーツに微細な穴が残りま す。焼結の工程(射出成形でもその温度と時 間は厳密に定義されています)により、残存す る結合剤が除去され、パーツは設計通りに、 仕上げ前のサイズと形状に収縮します。
プレス成形でも射出成形でも、この時点では まだ完成には程遠い状態です。ここから、現代 的なテクノロジーときめ細かな職人技による 最終的なフォルムの形成と装飾や仕上げ加工 という、骨の折れる緻密な作業が行われます。 ケース本体だけでも、最終的な形を作るのに かなりの労力を要します。手首に装着したり、 手に持った時、目に見えるのはケースの外観 だけで、ベゼルやムーブメント、ケースバックを 収める内部のパーツは見えませんが、表には 見えない基本パーツにも、何時間にも及ぶ研 磨作業が必要となります。サテン仕上げは、バ チスカーフの個性を際立たせる重要な美的 要素です。時計を近くでよく見ると、サテン仕 上げがいかに複雑で、洗練されたものかがよ くわかるでしょう。ケース側面には水平方向 に、ラグの間には垂直方向にサテン仕上げの ラインが入っています。
次の2つの数字は、手作業による仕上げの複 雑さを物語っています。ストラップを備えたバ チスカーフのセラミック製バックルに注目して みましょう。このバックルだけでも40以上の異 なるファセット(面)があり、仕上げ職人はファ セット一つひとつに丁寧に加工を施します。し かも多くの場合、一つのファセットにいくつも の工程が必要となります。ケースにはそれより もさらに多い、50以上のファセットがあり、そ れぞれに個別の仕上げが施されるのです。
新しいバチスカーフのセラミック製ブレスレッ トの製作にも、同様のイノベーションとディテ ールがふんだんに盛り込まれています。実際、 その製作工程からは2つの特許が生まれまし た。「マイヨン(maillon)」と呼ばれるブレスレ ットの各リンクは射出成形されています。射出 工程に続いて機械加工を行うため、セグメン トは最初はつまみが付いた状態で形成され、 その後、一つひとつ手作業で仕上げられ、サ テンのテクスチャーが与えられます。高級時計 のブレスレットの製造には、高い精度が求め られます。緩すぎるとブレスレットがたるんでし まい、逆にきつく締めすぎると、滑らかさがなく なるおそれがあるため、厳格な公差が設けら れており、適切なフィット感を確保するために リンクは1点ずつ注意深く測定、検証、調整さ れます。金属製であれセラミック製であれ、ブ レスレットのリンクをつなぐのは金属製のピン です。一般的に、時計のブレスレットのピンは ほとんどが円柱形をしていますが、ブランパン のセラミック製バチスカーフでは、より複雑な 形状を採用。特許を取得した、カムのような形 状のピンが、組み上がったブレスレットにほど よい柔軟性をもたらします。
またブランパンのセラミック製ベゼルの製作 にも、モデルごとに特有の難しさがありま す。70周年特別記念モデル、ACT 3のベゼル を例にとってみましょう。このモデルでは、12 時の位置に大きな三角形のインデックス、3 時、6時、9時の位置に数字、そして5分刻みの 表示にはバーインデックスが配されています。 これらのインデックスのくぼみはレーザーでカ ットされていますが、塗料の充填は手作業で す。特に難しいのは大きな三角形で、くぼんだ 部分の表面積が比較的大きいため、均一に 充填する難易度は高くなります。均一性を確 保するために双眼顕微鏡を使用しながら、イ ンデックス用のスーパールミノバを手作業で 塗布していきます。バチスカーフ クロノグラフ のベゼルのマーカーも同様に手作業で行わ れます。職人たちは、マーカー用の塗料を正 確に流し込めるよう特別に設計された支援ツ ールを使用してはいますが、例えば、数字の 「1」は「4」よりも塗料を若干減らすなど、細か な調整は専門家の判断に委ねられます。
さすがのブランパンも、開発時にジャーマンシ ェパードの顎の力までは考慮していなかった と思いますが、バチスカーフのセラミック製ケ ースやその他パーツには、硬度、耐傷性、軽量 性、肌へのなじみやすさ、そして幅広いカラー バリエーションなどセラミックの長所が存分 に活かされています。