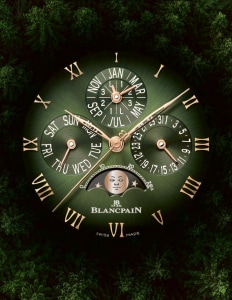
Kapitel 4
Ein Einblick in die Kunst der Uhrgehäusefertigung.
Das muss man der Uhrmacherzunft lassen: Sie kann sich einer Anerkennung erfreuen, die von allen Seiten kommt. Hochglanzmagazine, Social Media, das Internet, Fachzeitschriften, alle Welt feiert sie und ihre Handarbeit. Durch all das sind ihre Werkbänke, die famosen Établis, ins Rampenlicht geraten, dessen Scheinwerfer ihre Methoden, Techniken und sogar gelegentlich auch Geheimnisse enthüllen. Verkürzt gesagt: Sammler wissen, wie Uhrwerke gebaut werden und wie Uhrmacher arbeiten oder nehmen dies zumindest an. Aber wie sieht es mit den Gehäuseherstellern aus? Zweifellos nehmen Kenner die kleinsten Details von Design und Verarbeitung unter die Lupe und freuen sich, wenn sie ein exquisit gefertigtes Uhrgehäuse sehen und in der Hand halten können. Natürlich zu Recht. Eigentlich hat man ja eine engere Beziehung zum Gehäuse seiner Uhr als zu deren Werk. Denn obwohl dieses heute bei edlen Zeitmessern durch den Saphirboden bewundert werden kann, bleibt es doch in der Regel am Handgelenk zu 100 Prozent unsichtbar, außer wenn das Zifferblatt skelettiert ist. Das Gehäuse hingegen stellt sich sozusagen rund um die Uhr voll zur Schau. Seine Qualitäten sind denn auch offensichtlich und werden allgemein geschätzt. Doch wie steht es mit den Verfahren und Menschen, die diese Hüllen produzieren, die nicht nur schützen, sondern wesentlich zur Attraktivität einer Uhr beitragen? Es ist eine himmelschreiende Ungerechtigkeit, dass dieser wichtige Aspekt der Uhrmacherei weitgehend im Hintergrund bleibt, versteckt hinter einem Schleier. Lüften wir also den Schleier und erforschen wir die hohe Kunst der Gehäusefertigung.
Viele Kunstformen verschönern. Was als Leinwand begann, bleibt eine Leinwand. Dasselbe gilt für die Gravur. Ein graviertes Objekt behält seine Kernessenz. Die Gehäusefertigung hingegen ist ein transformativer Prozess. Ein Rohbarren aus Metall, sei es Gold, Platin oder Stahl, verwandelt sich in eine üppige Skulptur. Betrachtet man die fließenden Kurven und die schimmernde Politur des Gehäuses einer Uhr von Blancpain, ist es schwierig, ja fast unmöglich, sich vorzustellen, dass das einmal ein völlig reizloser Metallhaufen war. Bemerkenswert ist, dass diese Kunst, mit genügend Überblick gesehen, seit zwei Jahrhunderten im Wesentlichen gleich geblieben ist. Die mehr oder weniger rohe Grundform des Gehäuses wird maschinell produziert, gefolgt von aufwendiger Handarbeit für den letzten Schliff. Das heißt nicht, dass sich die Maschinen in dieser Zeit nicht weiterentwickelt hätten. Das war selbstverständlich der Fall. Ein Besuch im Hause Simon Et Membrez – dem Hersteller der Gehäuse für die Blancpain-Uhren und ebenfalls ein Unternehmen der Swatch Group – in der Stadt Delsberg/Delémont, dem Hauptort des Kantons Jura, beginnt denn auch stets mit einem Rückblick auf die Methoden der Vergangenheit.
Das Polieren der DoppelreifLünette einer Villeret-Uhr von Blancpain erfordert enormes Können, da einerseits ein vollendeter Glanz erreicht und andererseits die scharfe Kante bewahrt werden muss.
Es besteht ein auffälliger Zusammenhang zwischen der Geschichte der Gehäusefertigung und jener der Uhrwerke. So wie die Bauern im Schweizer Jura während der Wintermonate in den Wohnräumen über den Ställen ihrer Rinder und Pferde Uhrwerkkomponenten anfertigten, übten die Gehäusemacher ihr Handwerk als Schmiede und Schlosser unter ähnlichen Bedingungen aus. Soweit die Rohform der Gehäuseschalen nicht durch Gießen erzeugt wurde, stellte man sie anfänglich auf der handgetriebenen Spindeldrehbank durch Fräsen und Bohren her. In der zweiten Hälfte des 19. Jahrhunderts verlagerte sich die Herstellung der Gehäuse von der Heimarbeit in die Fabrik. Da in den USA die Industrialisierung weiter fortgeschritten war, entwickelten die Amerikaner als erste leistungsfähigere Stanz- und Drehmaschinen für die Verarbeitung der Metallplatten oder -blöcke zu Gehäusen von Taschen- und in der Folge Armbanduhren. Zu Beginn des 20. Jahrhunderts bauten die Schweizer die nächste Generation von Werkzeugen. Diese Maschinen wurden von einer obenliegenden, mit Riemenscheiben bestückten rotierenden Welle über Transmissionsriemen mit Kraft versorgt. Mit einer Batterie von Drehmeißeln bestückt, spanten sie die runden Details des Gehäuses aus runden Metallscheiben heraus. Die Messer der Meißel waren jeweils unterschiedlich geformt, um ein bestimmtes Element des Gehäuses zu bearbeiten. Bei diesem Verfahren wurde das rotierende Gehäuse gegen die starre Spitze des Drehmeißels gedrückt, wobei die Abspantiefe und der Vorschub präzise gesteuert werden konnten. Da die Werkzeuge nur für die Formgebung der runden Gehäuseelemente wie die Lünette (innen und außen), die inneren Auflagen für das Werk, den Gehäuseboden und andere feine Elemente konzipiert waren, wurden die Bandanstöße – die ja wirklich nicht rund sind – zu einem späteren Zeitpunkt angelötet.
Ebenfalls zu Beginn des 20. Jahrhunderts folgten weitere Fortschritte mit Maschinen, die stark genug waren, um Barren aus Messing, Gold, ja selbst Stahl oder Platin in die Grundform des endgültigen Gehäuses, einschließlich der Bandanstöße, zu prägen und zu stanzen. Die so erzielten Rohlinge wurden nach dem Stanzen durch Fräsen und Drehen sowie abschließend von Hand bearbeitet.
Die heutigen Verfahren stellen eine erneute Weiterentwicklung dar. Dazu gehört, dass es heute möglich ist, das Design des Gehäuses in jedem einzelnen seiner Details mit hoher Präzision am Computer fertigzustellen. Einige dieser Details sind großteils sichtbar: die Lünette, die Passung für das Uhrglas, der Innenring über dem Zifferblatt, der Übergang des Gehäuses zu den Bandanstößen und der Gehäuseboden. Vieles andere ist jedoch kaum sichtbar: die Innenflansche für das Uhrwerk, die Aussparungen für die exklusiven, von Blancpain patentierten Korrektoren unter den Bandanstößen und ihre Verbindungen zum Uhrwerk, die Öffnungen für die Krone, der Sitz des Zifferblatts in seiner Öffnung, die Aussparung, damit der Aufzugrotor genügend Spiel hat, und Elemente wie die Chronographendrücker sowie vieles mehr. Obwohl die Designer von Blancpain für all diese Details detaillierte Zeichnungen liefern, gibt es oft ein erhebliches Hin und Her für die Abklärung technischer Fragen, um sicherzustellen, dass das Gehäuse wie geplant und seinen Funktionen entsprechend produziert werden kann.
Eine historische GüdelGehäusedrehmaschine.
Polieren der Bandanstöße.
Ist das Design anhand von 3D-Entwürfen und Prototypen fertiggestellt und genehmigt, folgt als erster Produktionsschritt bei den meisten BlancpainGehäusen das Stanzen. Bevor es jedoch losgehen kann, müssen die Stanzwerkzeuge hergestellt werden. Bei Simon Et Membrez gibt es eine regelrechte Bibliothek von Werkzeugen, da diese für jeden Gehäusetyp von Blancpain einzigartig sind und spezielle Regale füllen. Bis zu 200 Tonnen Kraft werden eingesetzt, um die Rohform des Gehäuseoberteils mit seinen Bandanstößen zu stanzen. Diese hat zunächst streng geradlinige Kanten und Winkel. Um die feineren Formelemente zu erzeugen, erfolgten die unmittelbar nächsten Bearbeitungsschritte in den 1950er Jahren durch Zerspanen. Da jedoch dieses Abtragen von Material zwangsläufig etwas verschwenderisch ist, obwohl der Großteil der Späne und Körner zurückgewonnen wird, folgen heute auf das erste Stanzen mehrere weitere Stanzschritte, statt sofort zum Zerspanen überzugehen. Für bestimmte Elemente der Gehäuseform können bis zu zwanzig Durchgänge notwendig sein, wobei das Gehäuse oder Gehäuseteil dazwischen immer wieder gekühlt und neu erhitzt wird. Das Erhitzen in einer Wasserstoffatmosphäre konditioniert das Metall des Werkstücks für die weitere Formgebung.
Auf das Stanzen folgen aufwendige Dreharbeiten. Für runde Elemente arbeiten die heutigen CNC-Automaten, obwohl sie sehr fortschrittlich und programmierbar sind, im Grunde genommen ähnlich wie die Maschinen mit Riemenscheibenantrieb, die Anfang des 20. Jahrhunderts auf den Markt kamen. Nach wie vor wird das rotierende Gehäuse-Werkstück gegen die feststehende Spitze des abspanenden Drehmeißels gepresst. Auch bei diesen Drehautomaten gibt es eine Vielzahl von Meißelformen, die jeweils für ein bestimmtes Gehäuseelement konzipiert sind. Bei einem Blancpain-Gehäuse bearbeitet Simon Et Membrez übrigens nicht nur die eigentliche Gehäuseschale, sondern auch die Lünette und den Gehäuseboden auf diese Weise. Obwohl die Kernidee des Drehens von den Riemenscheibenmaschinen aus den Anfängen des 20. Jahrhunderts übernommen wurde, hat sich der Aspekt der Präzision innerhalb des Produktionsprozesses seither enorm weiterentwickelt. Für die damalige Zeit erreichten diese Maschinen eine bewundernswerte Präzision mit Feinjustierungen mittels Noniusverstellung, die eine genau kontrollierte Tiefeneinstellung des Drehmeißels ermöglichten. Heute jedoch können die Gehäuseelemente von Blancpain mit einer Toleranz von ± 3 Tausendstelmillimetern (Mikron) bearbeitet werden. Diese Präzision ist äußerst wichtig, um beispielsweise die Lünette in den Flansch des Gehäusekörpers, das Saphiruhrglas in die Lünette und den Saphirglasboden in die Gehäuserückseite einzupassen.
Bei manchen Blancpain-Uhren sind die Elemente des Gehäuses so kompliziert, dass die vielen unterschiedlichen Drehmeißel in einer einzigen Drehmaschine nicht ausreichen. Ein gutes Beispiel ist die Villeret Calendrier Chinois Traditionnel. Drei separate Maschinen mit jeweils anderer Meißelbestückung sind erforderlich, um alle notwendigen Dreharbeiten auszuführen.
Auch das Bohren von Löchern (französisch perçage genannt) besorgen Maschinen, die mit den Drehautomaten vergleichbar sind. Löcher im Gehäuse sind notwendig für die Krone, die Chronographendrücker, die Korrektoren in den Gehäuseflanken (bei Modellen ohne Korrektoren unter den Bandanstößen) sowie bei den Hörnern der Anstöße für die Federstege, an denen die Armbandteile befestigt sind.
Bislang waren alle Operationen darauf ausgerichtet, die Grundformen des Gehäuses (und separat die Lünette und den Gehäuseboden) sowie dessen innere und äußere Elemente herzustellen. Doch damit haben wir erst einen Bruchteil des Wegs auf unserer Reise zur Vollendung des Gehäuses zurückgelegt. Noch sind Dutzende von manuellen Gravier-, Schleif- und Polierarbeiten sowie die Montageschritte zu erledigen. Machen wir doch anhand einer Blancpain-Uhr einen Rundgang durch das Gehäuse, um einige der von Hand ausgeführten Operationen zu betrachten.
Ein guter Ausgangspunkt sind die Villeret-Bandanstöße. Die Form des Gehäusekörpers, der an die Bandanstöße grenzt, neigt sich zum Boden hin leicht nach innen. Dennoch ist die Passung zwischen dem Bandanstoß und dem abgerundeten Körper klar und scharf. Um diese exakte Verbindung zu erreichen, ist ein manuelles Schleifen erforderlich. Gearbeitet wird mit herkömmlichen runden Schleifsteinen. Mit geübtem Auge und Fingerspitzengefühl formt der Handwerker den feinen Rand der Kontaktstelle an der Kante des rotierenden Steins. Die innere Passung von Bandanstoß und Gehäusekörper wird in gleicher Weise ausgebildet.
Zwischen den verschiedenen Stanzschritten werden die Gehäuse erhitzt.
Polieren ist eine Kunst für sich. Unter speziellen Lampen, die so konzipiert sind, dass ihr Licht selbst kleinste Fehler hervorhebt, bearbeiten die Polierer nach und nach jede Oberfläche des Gehäusekörpers. Immer feinere Bürsten und Schleifmittel werden eingesetzt, um einen perfekten Glanz zu erzielen. Besonders heikel ist der Übergang zwischen dem Gehäusekörper und den Bandanstößen. Die ganze Sorgfalt, die auf diese Schnittpunkte an der Schleifscheibe verwendet wird, könnte leicht durch falsches Polieren beeinträchtigt werden. Nur die talentiertesten Gehäusepolierer sind in der Lage, die Schärfe der Verbindungsstelle vollständig zu erhalten und gleichzeitig den feinen Glanz zu erzielen, der das Markenzeichen eines Blancpain-Gehäuses ist.
Die unverwechselbare Doppelreif- oder DoublePomme-Lünette der Villeret-Modelle von Blancpain stellt eine besondere Herausforderung dar. Auch hier erfordert wieder eine Verbindung besondere Fähigkeiten, und zwar jene zwischen den beiden Ringen der Lünette. Der Polierer fixiert die Lünette auf einer speziellen Halterung und bearbeitet die Verbindung vorsichtig mit einer feinen Polierbürste. Denn die Kante muss sowohl scharf als auch rund um den 360-GradKreis der Lünette genau gleich bleiben. Nur Meister ihres Fachs mit jahrelanger Erfahrung werden mit diesem Veredelungsschritt betraut. Natürlich müssen auch die übrigen Oberflächen des Doppelreifs poliert werden, und die Anforderungen sind ähnlich: Es gilt, die perfekte Form zu bewahren und die Ringe gleichmäßig zu polieren.
Nach Abschluss der Polierarbeiten nimmt ein anderer Gehäusespezialist die Komponenten unter die Lupe. Im Licht einer Lampe, die selbst die kleinste Unvollkommenheit offenbart, wird das Stück genauestens examiniert und nötigenfalls zur erneuten Bearbeitung zurückgeschickt.
Kommen wir nun zu den Gehäusegravuren. Meist werden zwei Arten von Gravuren durchgeführt. Der Schriftzug BlancpaiN mit seinen relativ großen Lettern wird mit einem numerisch gesteuerten Fräskopf graviert, genauso wie die Gehäusenummer. Für kleinere Inschriften – etwa den Ausdruck swiss made oder die Referenznummer – verwendet man dafür heute einen Laser.
Das Polieren der Gehäuseelemente geschieht in sorgfältiger Handarbeit.
Je nach Modell gibt es spezielle Zusatzschritte. Viele der komplizierten Kalenderuhren von Blancpain sind mit den exklusiven und patentierten Korrektoren unter den Bandanstößen ausgestattet. Sie sind in Aussparungen auf der Gehäuseunterseite bei diesen „Hörnern“ eingebettet und ersetzen die traditionell verwendeten, in Nuten an den Gehäuseflanken untergebrachten Drücker. So bleiben die Stirnseiten der Blancpain-Uhren nicht nur perfekt glatt, diese Korrektoren ermöglichen dem Besitzer zudem, die Kalenderanzeigen jederzeit mit dem Fingernagel zu richten, ohne irgendeinen beim Kauf mitgelieferten Korrekturstift aus der Schublade holen zu müssen. Die Montage der Korrektoren unter den Bandanstößen ähnelt weitgehend derjenigen eines Uhrwerks. Die Schlitze und Nuten für die Korrektoren werden in das Gehäuse gefräst, bevor es auf die Werkbank des Monteurs gelangt. Das System besteht aus mehreren Komponenten, von denen die wichtigsten der kleine Drücker unter dem Bandanstoß, ein passendes Federsystem und eine winzige Halterung sind. Gewisse Blancpain-Modelle haben bis zu vier Korrektoren und die Uhr mit zusätzlichem chinesischem Kalender sowie jene mit einer Zeitgleichung sogar fünf, die jeweils von einem Spezialisten montiert werden.
Für die drehbaren Lünetten der Fifty-FathomsTaucheruhren sind spezielle Produktionsprozesse erforderlich, da diese in der Kollektion Fifty Fathoms aus bombiertem Saphir und bei den BathyscapheModellen aus Keramik bestehen. Die Saphir-Lünettenreife erhält Simon Et Membrez fertig in der Form, aber ohne Farbe sowie Indexe und Gradeinteilung. Als erster Schritt der Weiterbearbeitung wird ihre Unterseite mit einem von Blancpain entwickelten Verfahren eingefärbt. Diese Farbe verleiht dem leicht gewölbten Reif der Lünette einen einzigartigen Glanz und Reiz. Danach werden die Indexe und die Skalierung mit dem Laser graviert und mit Super-LumiNova® gefüllt. All dies geschieht ebenfalls von der Rückseite der Lünette her. Das Aufsetzen des Saphirreifs auf den Metallring der Lünette ist äußerst schwierig, da die
Montage der patentierten Korrektoren unter den Bandanstößen von Blancpain.
Montage der Lünette einer Fifty-Fathoms-Taucheruhr.
Toleranzen der Passung extrem klein sind. Zudem ist die Positionierung anspruchsvoll. Die Unterseite des Metallrings ist mit feinen Zähnen ausgestattet, die dafür sorgen, dass sich die Lünette in präzisen kleinen Schritten dreht. Die Schwierigkeit liegt darin, den fertigen Saphirreif in Bezug zu den darunterliegenden Zähnen so aufzusetzen, dass das Rhombus-Zeichen der Skala in der Grundposition direkt über 12 Uhr steht. Jede Abweichung nach links oder rechts ist inakzeptabel und würde die Tauchzeitmessungen verfälschen. Obwohl die keramischen Lünettenreife für die Bathyscaphe-Modelle bereits eingefärbt und mit ihren fertigen Skalen und Indexen aus Flüssigmetall bei Simon Et Membrez eintreffen, sind die Anforderungen beim Einsetzen in den Lünettenring vergleichbar.
Die Titangehäuse von Blancpain sind eine Kategorie für sich. Titan ist extrem hart und entsprechend schwierig zu bearbeiten. Beim Zerspanen nutzen sich die Messer der Drehmeißel besonders stark ab. Schon nach wenigen Durchläufen sind sie so stumpf, dass sie ausgetauscht werden müssen. Ein zweites, viel gravierenderes Problem ist die beim Drehen entstehende Hitze. Sowohl die Maschine als auch die Komponenten werden während der Bearbeitung extrem heiß, was zu einer nicht unerheblichen Brandgefahr führt. Daher müssen an den Fertigungsstandorten der Titangehäuse besondere Vorsichtsmaßnahmen getroffen werden.
Ist man einmal durch die Werkstätten des Gehäuseherstellers gegangen, in denen all diese Prozesse ablaufen, die ja aus Dutzenden und Aberdutzenden von Etappen für die Herstellung eines einzigen Gehäusetyps bestehen, dann schaut man ein Blancpain-Uhrgehäuse mit völlig neuen Augen an. Jetzt bewundert man bei den Bandanstößen, wie sie sich fließend an die Gehäuseflanken schmiegen, inspiziert die makellose Double-Pomme-Lünette eines Villeret-Modells oder spürt, wie die Drehlünette einer Fifty Fathoms, deren Rhombus-Index genau auf 12 Uhr zentriert ist, in der richtigen Position einrastet. Und da wird einem jedes Mal das imponierende Savoir-faire der Handwerker von Simon Et Membrez in Delsberg bewusst.