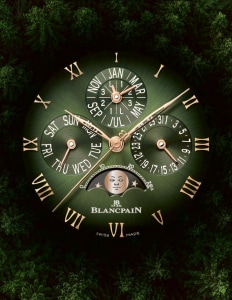
Kapitel 6
Das Material der Wahl, um hohe Festigkeit, geringes Gewicht, Korrosionsbeständigkeit und Verschleißfestigkeit zu kombinieren.
Die erste Regel der Abteilung Habillage von Blancpain1 (der Werkstatt für Gehäusefertigung) für die Verwendung von Titan bei der Bearbeitung lautet: geduldig und sanft sein. Ein Verstoß gegen diese Regel würde das Risiko bergen, dass sich dieses Metall ungeachtet seiner Festigkeit und Haltbarkeit während der Bearbeitung explosionsartig entzündet.
Angesichts der Unbeständigkeit der Götter in der griechischen Mythologie und der Herausforderungen, die sich bei seiner Bearbeitung stellen, ist esnicht verwunderlich, dass einer der beiden Entdecker des Titans (denn es gibt tatsächlich zwei Personen, denen dieser Fund zugeschrieben wird) das Metall nach dem Göttergeschlecht der Titanen benannt hat. Martin Heinrich Klaproth (1743–1817), der deutsche Chemiker, der seine Entdeckung „Titan“ taufte, nannte dieses chemische Element allerdings nicht wegen seiner Stärke und Haltbarkeit so – die damals noch nicht wirklich bekannt waren –, sondern wegen seiner Stabilität.2 Der zweite Protagonist der Geschichte, William Gregor, machte seine Entdeckung 1791 in Cornwall, England, unabhängig von Klaproth und wahrscheinlich vor ihm. Der Geistliche und Hobby-Mineraloge Gregor gab ihm den Namen „Menchanit“. Er war zwar der Erstentdecker, aber der Name Klaproths setzte sich durch.
Erstaunlich ist, dass Titan erst vor relativ kurzer Zeit Einzug in der Uhrenbranche hielt. Dieses Metall ist nämlich das neunthäufigste Element in der Erdkruste und kommt praktisch überall vor. Es ist nicht nur in fast allen Organismen enthalten, wir Menschen nehmen auch durchschnittlich 0,8 Milligramm pro Tag zu uns! Trotz der Allgegenwärtigkeit von Titan dauerte es nach seiner Entdeckung fast anderthalb Jahrhunderte, bis 1930 ein kommerziell nutzbares Verfahren zur Gewinnung des Titanerzes entwickelt wurde. Und noch länger, bis es Methoden für die Bearbeitung von Titan gab.
Dabei verliehen die Eigenschaften des Titans der Bewältigung der Schwierigkeiten bei seiner Gewinnung und Bearbeitung einen bemerkenswerten Schub. Sein Festigkeit/Dichte-Verhältnis ist höher als das aller anderen Metalle. Obwohl solider als kohlenstoffarmer Stahl, ist Titan 45 Prozent leichter. Darüber hinaus bietet es eine außerordentliche Korrosionsbeständigkeit, auch gegenüber Salzwasser, und behält seine silberne Farbe. Und schließlich ist Titan hypoallergen, ein wichtiges Kriterium, wenn es direkt auf der Haut getragen wird. Insgesamt ist dieses Material für alleVerwendungszwecke geeignet, bei denen man Robustheit, Leichtigkeit, Korrosionsbeständigkeit, Härte und Komfort kombinieren möchte. Kurz gesagt: Es vereint alle Eigenschaften, die für Sportuhren ideal sind.
1 Die Gehäuse und Armbänder der Blancpain-Uhren werden intern in den Habillage-Ateliers der Manufaktur hergestellt, die sich in Delémont (Delsberg) befinden, dem Hauptort des Kantons Jura unweit von Basel.
2 Diese Wahl ist etwas unpassend, denn der Mythologie zufolge waren die zwölf Titanen, ebenso wie ihr Vater Uranos und ihre Nachkommen alles andere als Musterbeispiele für Stabilität; sie schmiedeten ständig Intrigen und zettelten Kriege an.
Die verschiedenen Etappen bei der Herstellung von Bathyscaphe-Mittelteilen.
Ungeachtet der offensichtlichen Gründe für die Herstellung von Uhrgehäusen und -armbändern aus Titan, also für den Einsatz im Freien, wandte Blancpain Titan erstmals in einem Uhrwerk an. Als 2006 das erste Uhrwerk der neuen Generation, das Kaliber 13R0 mit Handaufzug und acht Tagen Gangreserve, eingeführt wurde, wählte man Titan als Werkstoff für die Unruh. Denn dank seines geringen Gewichts konnte der Energieverbrauch gesenkt werden, was wiederum zur Verlängerung der Gangautonomie beitrug.
Heute bietet Blancpain fünf Modelle mit Titangehäuse an, von denen zwei mit einem Titanarmband kombiniert werden können. Alle fünf stammen aus der Sportuhrenkollektion von Blancpain: je ein Air-Command-Chronograph als Herren- und als Damenuhr, zwei Bathyscaphe-Modelle, der vollständige Kalender mit Mondphase und die Automatikuhr, sowie als jüngste Version die Fifty Fathoms Tourbillon.
Diese fünf Uhren in Titan unterscheiden sich von den anderen Zeitmessern mit Titangehäusen der Uhrenindustrie dadurch, dass Blancpain die unter der Bezeichnung Grade 23 bekannte exklusivste Titanlegierung verwendet, die nur sehr geringe Einschlüsse enthält. Da reines Titan für die Herstellung von Uhren nicht ideal ist, werden seine Eigenschaften durch kleine Zusätze von Aluminium (6 %) und Vanadium (4 %)3 verbessert. Die so entstandene Legierung wird gemeinhin als Grade 5 bezeichnet. Manche bezeichnen sie auch als „medical grade“, da sie sich besonders gut für den medizinischen Gebrauch eignet, vor allem für den Gelenkersatz. Das von Blancpain verwendete Titan Grade 23 ist eine Variante des Titans Grade 5. Der Unterschied liegt in der Reinheit, wobei Grade 23 reiner ist, weil es weniger Sauerstoff enthält. Um als „Grade 23“ bezeichnet zu werden, darf die Legierung einen maximalen Sauerstoffanteil von 0,13 % nicht überschreiten. Dieser geringere Anteil verbessert die Bruchfestigkeit des Metalls, das aufgrund seiner Festigkeit, seines geringen Gewichts, seiner Korrosionsbeständigkeit und seiner Härte zur ersten Wahl wird. All diese Vorteile haben Blancpain bewogen, für seine Zeitmesser Titan Grade 23 zu wählen.
Den Preis für die vielen Vorzüge des Titans bezahlt man bei der Herstellung der Gehäuse oder Armbänder aus diesem Metall. Denn die beim Endprodukt höchst erwünschte Härte und Festigkeit des Titans erschweren die Bearbeitung und das Polieren im Vergleich zu Stahl oder Gold bei weitem. Obwohl Blancpain seine Gehäuse aus Titan in denselben Werkstätten wie die aus den anderen Metallen produziert, müssen für die Bearbeitung von Titan andere Maschinen und Verfahren eingesetzt werden.
3 Vanadium ist wie Titan ein Übergangsmetall. Der Begriff Übergang bezieht sich auf seine Position im Periodensystem der Elemente. Vanadium kommt in der Natur weit verbreitet vor, wenn auch nur in mikroskopisch kleinen Mengen. Man findet es in schwarzem Pfeffer, Meeresfrüchten, Petersilie oder auch Getreide.
Alles beginnt damit, dass die Rohform des Gehäuses, einschließlich der Hörner oder Bandanstöße, aus einer Titanplatte von zuvor festgelegter Höhe ausgeschnitten und auf eine hohe Temperatur erhitzt wird. Bei einem Gehäusemittelteil aus Gold oder Stahl wird üblicherweise ein Stanzverfahren angewandt, was bei Titan absolut nicht möglich ist. Die Details des Schneidprozesses sind ein streng gehütetes Produktionsgeheimnis. Die exakten Parameter der Temperaturen, Umgebungsatmosphäre, Abkühlzeiten und Stanzwerkzeuge spielen eine wichtige Rolle. Im Prinzip wird die Titanplatte mehrmals bearbeitet. Auf jeden Temperaturanstieg in einer bestimmten Atmosphäre folgt eine Abkühlungsphase. Diesen Zyklus, mit dem das Material konditioniert wird, bezeichnen Metallurgen als „Glühen“. Das Ergebnis dieser Arbeitsschritte ist ein Rohgehäuse mit integrierten Hörnern. Der Gehäuseboden aus Titan und die Lünette können in einem anderen Verfahren hergestellt werden. Diese Komponenten können aus einem runden Titanstab gefertigt werden. Der Erhitzungs- und Abkühlungszyklus vor der Metallbearbeitung bleibt notwendig, um Gewähr für deren Qualität zu leisten. Ein Verzicht auf das Glühen würde aufgrund der hohen inneren Spannungen zu Verformungen beim weiteren Bearbeiten führen.
Was in der Blancpain-Abteilung Habillage folgt, erfordert nicht weniger Know-how als die Phasen des Schneidens und Glühens. Beim Drehen eines Gehäusemittelteils kommt als erster Bearbeitungsschritt ein Drehmeißel mit Wendeplattenmeißel zum Einsatz für den Innendurchmesser, der während des gesamten Herstellungsprozesses als Referenz dient. Im Großen und Ganzen ähnelt dieser Prozess dem vor über hundert Jahren üblichen Verfahren zur Bearbeitung von Dosen und ist auch für das Drehen der Gehäuse aus Stahl oder Gold identisch. Beim Titan ist jedoch einiges anders. Da ist zunächst einmal das Kühlen des Schneidewerkzeugs. Die ölhaltige Lösung, die bei der Bearbeitung anderer Materialien verwendet wird, ist für Titan aufgrund der durch das Schneidewerkzeug verursachten hohen Temperatur nicht zu empfehlen. In diesem Fall wird daher eine Lösung auf Wasserbasis bevorzugt. Dennoch bleibt die Brand- und Explosionsgefahr bestehen. Deshalb sind alle Bearbeitungszentren mit leistungsstarken Sicherheitssystemen ausgestattet, die Flammen im Bruchteil einer Sekunde erkennen und löschen können, um einen größeren Schaden zu verhindern.
Die vielen verschiedenen Metallbearbeitungsschritte sind durch die Details des Gehäusedesigns vorgegeben. Für jedes Element des Gehäuses sind spezielle Schneidewerkzeuge erforderlich, und bei jedem Fertigungsschritt müssen extrem strenge Toleranzen eingehalten werden. Dies gilt für alle Blancpain-Uhren, ist aber bei Taucheruhren wie der Fifty Fathoms und der Bathyscaphe wegen der hohen Anforderungen an die Wasserdichtigkeit besonders wichtig. Präzision ist das oberste Gebot, um sicherzustellen, dass der Boden, die Lünette und die Dichtungen perfekt zum Gehäusemittelteil passen.
Weitere Arbeitsschritte folgen. Eine wichtige Phase ist das Bohren von Löchern, einerseits für den Kronenschaft im Gehäusemittelteil, andererseits für den Armbandsteg. Beim Chronographen Air Command sind zusätzliche Löcher für die Integration der Drücker erforderlich. Die Bearbeitung der Gehäuse durch Fräsen erfordert denselben Grad an Präzision wie das Drehen. Es gilt die gleichen Vorsichtsmaßnahmen und besonderen Vorkehrungen gegen die Entflamm- barkeit und/oder mögliche Explosionen zu treffen.
Es wird auch ein Schleifvorgang durchgeführt. Um perfekt saubere Übergänge zwischen den Hörnern und dem Mittelteil zu schaffen, wird letzteres beidseitig geschliffen. Neben der Sauberkeit der Übergänge muss auch darauf geachtet werden, dass die Innenseite der Hörner flach und gerade bleibt. Diese Endbearbeitung erfolgt an einer rotierenden Schleifscheibe und erfordert viel Geschick und Erfahrung, um eine saubere und glänzende Verbindung zwischen den Hörnern und dem geschwungenen Mittelteil zu erzielen.
Nach Abschluss dieser zahlreichen Arbeiten an Dreh- und Schleifmaschinen sind die handwerklichen Berufe der Endbearbeitung an der Reihe, etwa beim manuellen Polieren.
Die Endbearbeitung war schon immer eine Aufgabe für hochqualifizierte Spezialisten, insbesondere wenn die zu bearbeitenden Formen komplex und die Texturen vielfältig sind. Bei den Titanmodellen der Fifty Fathoms werden sämtliche Oberflächen des Gehäuses satiniert. Die Herausforderung für die Handwerker, die diese Veredelung vornehmen, besteht darin, sicherzustellen, dass die feinen Rillen auf den satinierten Oberflächen sowohl in Bezug auf die Tiefe als auch auf die Ausrichtung einheitlich sind. Zusätzliche Sorgfalt ist dort erforderlich, wo die Bandanstöße auf das Gehäuse treffen. Die Satinierung darf die scharfe Kante der zuvor bearbeiteten Verbindungsstelle nicht beeinträchtigen.
Die Herren- und Damenuhren der Air Command sind eine weitere Herausforderung für das Geschick bei der Endbearbeitung. Die Bandanstöße haben sowohl eine polierte als auch eine satinierte Oberfläche. Der Winkel zwischen den beiden Oberflächenarten muss perfekt definiert bleiben. Das kann man nur sicherstellen, indem man jeweils eine der beiden Flächen mit einer Kunststoffschutzfolie abdeckt, während die andere bearbeitet wird.
Eine lange Liste zusätzlicher Schritte betrifft die Herstellung der Drehlünetten und Gehäuseböden. Eine drehbare Lünette ist ein wesentlicher Bestandteil von Taucher- und Fliegeruhren. Sie ist gerändelt, um das Drehen zu erleichtern, vor allem mit Handschuhen. Alle Lünetten sind mit einem Einsatz ausgestattet, der die Markierungen anzeigt. Bei den Modellen Bathyscaphe und Air Command besteht dieser aus Keramik, bei der Fifty Fathoms Tourbillon aus gewölbtem Saphir.
Das Polieren der Gehäuseflanken einer Fifty Fathoms ist ein komplexer Vorgang, der höchste Präzision und Fertigkeit erfordert, um eine perfekt saubere Verbindung zwischen den Hörnern und dem Mittelteil zu erzeugen.
Für diesen Einsatz muss auf dem Drehautomaten eine Nut gebohrt werden. Die Toleranzen bei diesem Verfahren sind äußerst präzise, damit der Keramik- oder Saphireinsatz passgenau ins Metall eingesetzt werden kann. Außerdem sind die Lünetten von Taucheruhren rückseitig millimetergenau mit sehr feinen Zähnen bestückt. Diese Zähne sind Teil des Mechanismus für das einseitige Drehen und werden in die Lünette eingraviert.
Parallel zur Markteinführung dieser neuen Modelle präsentierte Blancpain Titanarmbänder für die drei Bathyscaphe-Modelle und die Fifty Fathoms Tourbillon. Sie sind als erste Bänder dieser beiden Linien aus Titan Grade 23 gefertigt worden. Davon abgesehen geht ihr Stil auf die 1990er Jahre zurück und ist emblematisch für Blancpain. Kenner werden sofort die Handschrift der für ihre Eleganz und ihren Tragekomfort bekannten klassischen „71er“-Stahlarmbän-der von Blancpain erkennen.
Das Mittelteil einer Fifty Fathoms.