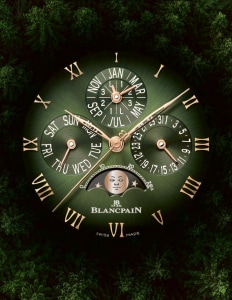
Capítulo 4
La mejor manera de hacerse a la idea de cómo se construye un brazalete refinado es pensar en la complejidad de la Alta Relojería.
Villeret Quantième Complet.
Quinientos treinta y un componentes. Ensamblaje artesanal hecho a mano y elegantes acabados meticulosamente ejecutados por expertos artesanos. Parece la descripción de un gran movimiento con complicaciones, pero no: se trata del brazalete Mille Mailles de Blancpain, hecho en acero u oro. Este paralelismo con la Alta Relojería no se limita a la descripción anterior, sino que se puede aplicar a todo el proceso de creación de un brazalete refinado.
Puesto sobre la mano, el brazalete Blancpain Mille Mailles revela poco de la complejidad de su diseño y mucho menos de los elaborados pasos seguidos para su construcción. Ni tiene por qué hacerlo. Por encima de todo, un brazalete haut de gamme se distingue por todo lo que no tiene: ni rastro de mal ajuste en la muñeca, ninguna traba a su flexibilidad, ausencia de desproporciones en sus acabados, ningún desequilibrio en su ponderación ni ningún hueco en el flujo de sus componentes. Si el brazalete da lugar a algún pensamiento, ciertamente debe estar en la línea de “¿cómo puede un objeto de metal ser tan flexible y resistente al mismo tiempo?”.
En la mano o en la muñeca, los refinados y brillantes acabados del brazalete no revelan sus secretos. Aunque no lo parece cuando se usa, su construcción es compleja y exige una disposición estudiada de once eslabones interiores diferentes y veinte exteriores, denominados en francés “maillons”. Incluso un escrutinio visual cercano revela tan solo una pequeña parte de las diferencias entre eslabones. Únicamente si se tiene la oportunidad de presenciar su ensamblaje o de estudiar los dibujos de los maillons es posible ver claramente que no todos son iguales, más aún, que hay 31 tipos y tamaños distintos. No sorprende que sea tan difícil catalogar las diferencias, ya que a menudo son muy sutiles, de fracciones de milímetro, y hace falta una vista de lince incluso si se ponen uno al lado del otro y se comparan.
También queda oculta a la vista la manera en que los componentes se unen entre sí. Los maillons se enlazan unos con otros con unos pasadores finos anclados a cada lado y a lo largo del brazalete formando hileras. De esta manera, los eslabones se mantienen invisiblemente en su lugar pero conservan cierto movimiento, es decir, forman parte de una cadena pero pueden adaptarse a la forma de la muñeca.
Aunque se entiendan totalmente los principios básicos de su construcción y se observen de cerca los distintos elementos, incluyendo la forma en que el brazalete se flexiona, los procesos minuciosos de ensamblaje y acabado están lejos de ser revelados. Para descubrir el misterio de cómo se juntan estos más de 500 componentes es preciso viajar al extremo norte de Suiza, cerca de la frontera con Francia, en concreto a la ciudad de Delémont, donde se encuentra Simon & Membrez, compañía hermana de Blancpain.
Por supuesto, el proceso comienza con la fabricación de los componentes. Las tolerancias son microscópicas, del orden de 5 micras. Si bien esto puede sonar extremo, se requiere esta alta precisión para que cada eslabón se ajuste con exactitud y a la vez permita la flexión del conjunto. Los componentes llegan al banco de trabajo del ensamblador ya ordenados por tipos, cada uno en un pequeño contenedor numerado (el número indica el tipo de componente). Hay que tener en cuenta que en total hay 31 tamaños y tipos diferentes. La numeración de los contenedores es importante, ya que solo los eslabones que incluyen tornillos que se pueden quitar fácilmente con un destornillador para ajustar el brazalete a la muñeca del propietario se distinguen a primera vista del resto.
El primer paso es fijar los pasadores a los eslabones laterales que se extienden a lo ancho del brazalete formando las filas. Cada pasador se mantiene firmemente en su lugar gracias a un ajuste firme en el orificio perforado y al uso de un pegamento.
Nada queda al azar. A pesar de que los pasadores tienen un doble sistema de sujeción (ajuste firme y pegamento), se somete a prueba el pegamento. Cuando llega un nuevo lote se utiliza una muestra para fijar un pasador a un maillon y se mide la fuerza necesaria para separarlo. Por supuesto, esa fuerza supera con creces cualquier circunstancia a la que el brazalete se pueda ver expuesto mientras se usa. Una vez validado por la prueba, el pegamento de ese lote pasa a ser usado en el proceso de producción.
Completado el encolado, los eslabones laterales, ahora con los pasadores bien sujetos, se disponen y ordenan por tamaño tal como quedarían en el brazalete terminado. A continuación, el especialista enrosca cada uno de los once eslabones interiores de diferentes tamaños en los pasadores. Colocar los maillons correctos en cada ubicación es fundamental. En general, cada fila tiene un solo tamaño de eslabón, pero hay excepciones, como las cuatro filas que se pueden quitar con un destornillador (las que tienen tornillos en el exterior para facilitar el ajuste a la muñeca). Estas filas tienen una mezcla de dos tipos diferentes de eslabones interiores. Para ayudar en el proceso existe una herramienta especial que permite sujetar el ensamblaje, con cada ubicación numerada para que se corresponda con el tamaño particular de los eslabones que van en esa posición concreta del brazalete.
Cuando todos los eslabones interiores se han enroscado en los pasadores se colocan los eslabones exteriores. El sistema es el mismo que para el primer lado: ajuste firme en el orificio perforado y pegamento.
En este punto el brazalete está ya en buena medida ensamblado. Solo le falta el componente que lo une a la caja del reloj en un extremo y a la hebilla en el otro. Blancpain exige que sus relojeros se encarguen de unir el brazalete al reloj, por lo que se les envía el brazalete junto con un componente llamado “attache boîte”. La hebilla está unida en cada extremo a maillons con el mismo sistema de tornillos que las filas extraíbles. Aunque el ensamblaje podría acabar aquí, a falta solo de sujetar el brazalete al reloj, la fabricación está lejos de tocar a su fin. Todavía nos espera el acabado, que presenta sus propios y singulares desafíos.
Para empezar, lograr un brillo perfecto de los maillons teniendo en cuenta el espacio extraordinariamente restringido entre cada fila, exige técnicas especiales. El responsable de los acabados dobla el brazalete hacia atrás fila por fila para exponer al máximo los lados interiores de los maillons. De esta forma puede acceder a cada lado del espacio entre las filas. A continuación, cada par de filas se presiona sobre un cepillo rotatorio de pulido extrafino que tiene el romántico nombre “la brosse moustache” (cepillo de bigote). La reducida anchura del “bigote” se ha concebido para permitir que sus cerdas actúen en el espacio restringido entre las filas. Este proceso se repite cada par de filas, una por una. Cuando se han pulido todas con el “bigote”, los espacios interiores lucen ya un brillo perfecto.
El siguiente paso nos lleva a los lados del brazalete. Aquí hay dos cuestiones importantes. Obviamente, hay que conseguir un brillo perfecto, pero también mantener la superficie perfectamente plana. Una estudiada técnica satisface ambas exigencias. El brazalete se coloca plano sobre un soporte y a continuación se presiona lateralmente sobre el lado plano de un disco de pulido orientado en ángulo recto al brazalete. De este modo, todo el lado se pule contra la superficie plana del disco de pulido, obteniendo el acabado deseado y manteniendo la planitud.
Tras pulir los lados contra el disco plano, el trabajo de acabado regresa a la superficie superior para dar mayor lustre a los lados. Se utilizan una serie de tres cepillos de pulido diferentes, de menos a más suave. A medida que el trabajo avanza de cepillo en cepillo, los compuestos de pulido empleados son cada vez más finos. Aunque el pulido final de los lados se puede lograr deslizándolos contra los tres cepillos de pulido diferentes, la superficie superior exige un tratamiento fila por fila. De manera similar a la técnica empleada con el “bigote”, el brazalete se dobla sobre sí mismo de modo que solo se presione una fila contra el cepillo. Empezando con la fila más exterior, toda la longitud del brazalete se va puliendo contra la sucesión de pinceles.
Esto nos deja solo la superficie interior. Aquí, en lugar de un pulido brillante, los criterios estéticos exigen un acabado satinado, lo cual tiene sus propias particularidades y desafíos. Primero, las líneas extraordinariamente finas que son la esencia del satinado se logran moviendo el brazalete de adelante hacia atrás contra la rueda abrasiva. Es preciso mucho cuidado para garantizar que las líneas, que se extienden a lo largo, sean perfectamente rectas y consistentes. Lo que hace que la tarea sea aún más exigente es la presencia de dos pequeñas áreas con un pulido brillante en la parte posterior: la primera, en el extremo más alejado del brazalete; la segunda, un borde fino que se extiende a lo largo de los bordes más alejados a medida que la parte posterior se curva hacia arriba a los lados de unos maillons muy pulidos. Estas dos zonas con un pulido brillante se aplican después del acabado satinado. En cuanto a la pieza final, se utiliza un clip para sujetar el brazalete con precisión contra la rueda de pulido, de modo que el borde entre brillante y satinado quede correctamente colocado. Idéntica habilidad se requiere para exponer a la rueda solo la zona a pulir y otorgar brillo a la zona estrecha de transición entre la parte trasera y los lados de cada maillon.
Lo que queda es un paso final con un cepillo de pulido extremadamente flexible, orientado en dos direcciones para garantizar que no haya líneas de pulido en las superficies brillantes. Después viene la limpieza. Cada brazalete se inspecciona meticulosamente bajo una iluminación especial para verificar su perfecto acabado.
Aunque el Mille Mailles es el que tiene un mayor número de componentes, el ensamblaje y acabado de otros brazaletes de Blancpain, como el legendario 71 y el Bathyscaphe, siguen procesos similares. Los seguidores de Blancpain conocen el largo linaje histórico del 71, que remonta a dos décadas, es decir a los inicios del primer cronógrafo Flyback. En una época en que los brazaletes de los relojes deportivos eran rígidos en aparentemente todos los lugares equivocados y no se adaptaban cómodamente a la muñeca, el 71 fue una revelación. Su diseño flexible y el perfecto ajuste fueron revolucionarios y lo convirtieron en el modelo a seguir para los brazaletes metálicos. Su secreto radica en las formas sutilmente redondeadas de sus eslabones y piezas de borde, así como en la posición de los pasadores, que van de lado a lado y mantienen los elementos unidos.
Los brazaletes 71 y Bathyscaphe tienen un acabado cepillado. Aunque están formados por menos componentes y menos variados que el Mille Mailles, su montaje y acabado son igualmente exigentes. Los principios básicos para su construcción son los mismos. Los elementos se conectan mediante pasadores, firmemente ajustados y pegados a los componentes exteriores, colocados a lo largo del brazalete, conectados a los componentes interiores y luego fijados al extremo exterior. Los componentes reciben un primer cepillado antes de ser ensamblados. Después se les da un toque final sosteniendo el brazalete contra una correa giratoria con un abrasivo que se adapta a la finura deseada de las líneas de las superficies cepilladas. Este toque final es extremadamente exigente, ya que hay que garantizar que las líneas estén perfectamente rectas y orientadas con precisión a lo largo del brazalete.
La relojería, en todas sus dimensiones, siempre ha puesto a prueba a quienes la practican, que deben cumplir con los más altos estándares de la artesanía. Por lo tanto, no es sorprendente que la creación de un brazalete metálico de prestigio tenga una exigencia análoga a la creación de movimientos, esferas y cajas. •