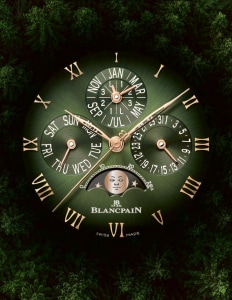
Capítulo 5
Introducción de la cerámica de alta tecnología en el mundo de la relojería.
La curva de innovación en relojería se ha mantenido ascendente durante varios siglos. No siempre lo ha hecho, sin embargo, con la misma pendiente ni centrada en las mismas cuestiones. Algunas épocas se han visto marcadas por nuevos diseños mecánicos. Otras, por oficios artísticos. Y otras, por la estética. Lo que sí ha sido una constante a lo largo del tiempo es la innovación en el ámbito de los materiales, que ha propulsado avances en cronometría (materiales para espirales, volantes, rubíes o ruedas), robustez (rubíes o el cristal del reloj) e incluso arte (nuevos ingredientes artesanales).
Hoy en día, en un momento en que las veneradas complicaciones y construcciones reflejan diseños que fueron pioneros en relojes de bolsillo hace dos siglos, los nuevos materiales siguen desempeñando un papel destacado en el panorama de la innovación. La devoción de Blancpain por la creación ha situado a la Manufactura a la vanguardia a la hora de incorporar nueva tecnología de materiales a los diseños de sus relojes. He aquí algunos ejemplos: espirales de silicio; membranas de metal líquido; ruedas hechas mediante LiGA; aleaciones para los muelles de alto rendimiento; aleaciones especiales de titanio para volantes, cajas y brazaletes; cajas de oro bronce; y mucho más. En esa lista, la cerámica para cajas, biseles y, ahora, brazaletes ocupa un lugar destacado.
Existen buenos motivos que justifican la adopción actual de la cerámica en relojería. Si tuviera que poner negro sobre blanco la lista de los atributos que la cerámica aporta a la fabricación de cajas y brazaletes, la enumeración sin duda incluiría la durabilidad, la resistencia a los arañazos, la ligereza, las propiedades hipoalergénicas y una amplia variedad de colores. La cerámica no solo cumple con todos estos requisitos, sino que ningún otro material usado en cajas y brazaletes la supera. Fijémonos, por ejemplo, en la durabilidad y la resistencia a los arañazos. La medida estándar sería la dureza expresada en la escala de Vickers. El acero inoxidable convencional alcanza una dureza de 250 Vickers; el oro, de 100 Vickers; el titanio grado 23, de 300 Vickers. La cerámica de dióxido de circonio los supera a todos con 1200 Vickers.
Para poner esos 1200 Vickers en perspectiva, tomemos una historia real. Un buen día deposité mi Bathyscaphe de cerámica sobre el escritorio de mi oficina para atender otros asuntos, dejando a mi pastor alemán de más de cuarenta kilos a cargo de la habitación. Al regresar, encontré trozos de la robusta correa de lona esparcidos por todos lados y el reloj, que claramente había sido objeto de las travesuras del perro, en el suelo. Para mi deleite, al examinarlo con una lupa de relojero no encontré ni siquiera un atisbo de rasguño o defecto en el reloj, lo cual, por otra parte, no fue una sorpresa para este científico de materiales. Los 1200 Vickers superaron fácilmente las «caricias» de las mandíbulas de un pastor alemán grande. Puntuación final: caja de cerámica 1, perro 0.
Bathyscaphe Quantième Complet Phases de Lune
Cuando se trata de ligereza, la cerámica vence igualmente a su «competencia». Es casi un 70% más ligera que el oro y un 25 % más que el acero1. Alguien podría argumentar que el oro ofrece una amplia gama de colores: amarillo, diferentes tonos de rosa/rojo y blanco. Pero la cerámica tiene unas posibilidades cromáticas prácticamente ilimitadas. La colección actual de Blancpain incluye tonos gris plasma, negro, azul, blanco y verde.
Si se toman en cuenta estos atributos tan atractivos, ¿por qué la industria relojera no ha adoptado la cerámica de una forma más amplia? La respuesta es simple: elaborar cajas y brazaletes de cerámica es tremendamente complejo, exasperantemente difícil con respecto al nivel de detalle y extraordinariamente exigente en cuanto a los acabados artesanales. Solo unos pocos dominan el savoir-faire necesario para producir los componentes y aún son menos los que cumplen con los exigentes estándares de la prestigiosa relojería de alta gama. Un recorrido por el taller de cerámica ubicado en Le Locle, a escasos metros de la frontera francosuiza, permite descubrir tanto la ciencia de los materiales como el talento artesanal que intervienen en la creación de los relojes de cerámica de Blancpain.
En muchos sentidos, afirmar que la cerámica se usa básicamente en «cajas» y «brazaletes» es simplificar demasiado. Tomemos, por ejemplo, la caja de cerámica del Bathyscaphe Chronographe de Blancpain. No solo el cuerpo de la caja está fabricado con cerámica, sino también el bisel, el fondo de la caja, los pulsadores del cronógrafo y la corona. Asimismo, la hebilla de la correa es del mismo material. En la versión, recientemente presentada, con brazalete de cerámica, solo la hebilla desplegable es de titanio. Para cada uno de estos elementos se aplican diferentes procesos. Para el cuerpo, el bisel y el fondo de la caja se emplea un proceso de prensado; para el resto de componentes, como la corona, los pulsadores del cronógrafo y los eslabones del brazalete, se realiza un proceso de inyección. A pesar de las diferencias entre los dos procesos, ambos tienen algo en común: son asombrosamente exigentes en cuanto al nivel de detalle y los acabados aplicados a mano.
1 La cerámica pesa aproximadamente 6 g/cm3, el oro 19,3 g/cm3 y el acero inoxidable, 8,03 g/cm3.
Los dos procesos parten del polvo de dióxido de circonio (ZrO2). Este polvo es blanco, por lo que, para conseguir el espectro de colores que podemos encontrar en la colección de Blancpain (negro, gris plasma, azul, verde, etc.), el segundo paso consiste en mezclar el polvo de circonio con al menos un pigmento de alta tecnología. Por trivial que parezca, hay una gran cantidad de parámetros que entran en juego en esta parte del proceso y que requieren de un estudio cuidadoso y de mucha precisión para llegar al tono deseado. No solo la proporción entre pigmento y polvo está estrictamente definida, sino que también la selección del material del pigmento se realiza tomando como base la experiencia en la ciencia de materiales. Dado que, más adelante, se procederá al horneado a alta temperatura, se debe tener en cuenta cómo el calor afecta al color. Un ejemplo: el pigmento de la cerámica negra es gris o tostado antes de calentarlo. La selección de pigmentos de alta tecnología requiere mezclar una variedad de ingredientes cuyo color se desarrollará durante la sinterización, un proceso de calentamiento al que nos referiremos en el siguiente párrafo. Es necesaria una ingeniería cuidadosa para perfeccionar el paso de la pigmentación y llegar al tono deseado de manera predecible y duradera. La pigmentación concluye con la molienda húmeda del polvo y el pigmento para asegurar una mezcla adecuada a fin de cubrir cada grano de polvo con pigmento.
Es en este punto donde los procesos de prensado e inyección toman caminos diferentes. Para prensar, se añaden múltiples aglutinantes que dan como resultado un polvo húmedo. Posteriormente, la mezcla se prepara en un proceso de atomización y secado por aspersión. El polvo así preparado se deposita en una herramienta en una cantidad medida con precisión y se prensa a alta presión. Nuevamente, los parámetros son complejos: el grado de presión (¡varias toneladas!), los ciclos en la herramienta, etc. Incluso la geometría de la herramienta es producto de un cuidadoso estudio, ya que el paso posterior a la compresión, llamado sinterización, reducirá el tamaño. Sinterizar significa hornear a una temperatura alta preestablecida durante un tiempo definido precisamente por la temperatura, el período y el ritmo durante el cual se aumenta el calor, así como por la duración (varios días). Al igual que sucede con prácticamente todos los elementos de los relojes finos, y en particular con aquellos relacionados con la resistencia al agua, el proceso debe controlarse de manera rigurosa para producir unas dimensiones finales precisas dentro de unos estrictos márgenes de tolerancia.
El color gris plasma exige un proceso de calentamiento adicional. Los componen- tes se someten a un tratamiento térmico de plasma ultraalto que transforma el óxido de circonio en carburo de circonio. Dicha transformación da como resultado un color gris plasma único que se parece mucho al acero inoxidable.
Los componentes producidos por inyec- ción viajan por una ruta ligeramente diferente. Después de la «molienda húmeda» del polvo combinado con el pigmento de alta tecnología, la mezcla se seca por aspersión y se atomiza. En un ambiente controlado se incorporan múltiples aglutinantes patentados al polvo coloreado para completar la mezcla. Luego, esta combinación se tritura y granula hasta adquirir un tamaño preestablecido que facilita y prepara la inyección.
Los propios moldes son producto de una intensa labor de ingeniería. Por supuesto, la geometría debe tener en cuenta la contracción que se producirá más tarde, así como la estructura y posición del punto de inyección. Dado que quedará un pequeño resto de la inyección, románticamente denominado «zanahoria», la posición debe estar en un lugar que facilite su eliminación. Después de la inyección, los aglutinantes patentados se eliminan parcialmente de forma química, dejando agujeros microscópicos en el componente cerámico. La sinterización, también con temperaturas y tiempos definidos con exactitud, elimina los aglutinantes restantes y deja el componente en el tamaño y forma que se han diseñado para el preacabado.
En esta etapa, tanto los componentes prensados como los inyectados están todavía lejos de su acabado final. Queda una labor de precisión en la que intervienen tanto tecnologías modernas como trabajos manuales minuciosos para conseguir las formas y acabados finales.
En el caso de la caja propiamente dicha, hace falta un trabajo considerable para darle la forma final. En la muñeca o en la mano, la caja solo revela sus formas exteriores. No se puede apreciar el interior, donde se alojan el bisel, el movimiento y el fondo de la caja. Se necesitan horas de pulido para dar forma a estos elementos esenciales. Los acabados satinados son un elemento estético importante que distingue al Bathyscaphe. Un examen detenido del reloj muestra la complejidad y sofisticación de estos acabados. Los laterales de la caja presentan finas líneas satinadas orientadas horizontalmente; entre las asas, en cambio, la orientación es vertical.
Dos datos ilustran la complejidad de los acabados aplicados a mano. La hebilla de cerámica de los Bathyscaphe equipados con correa, por ejemplo, tiene más de 40 facetas distintas que los artesanos del acabado deben abordar una a una, a menudo varias veces. Por su parte, la caja tiene más de 50 facetas, cada una de las cuales requiere un acabado independiente.
Detalles similares abundan en la creación del nuevo brazalete de cerámica del Bathyscaphe, también un ejemplo de inno- vación. De hecho, el proceso ha dado lugar a dos patentes. Cada uno de los eslabones del brazalete, denominados maillons, es inyectado. Los segmentos se forman inicialmente con una pestaña para realizar el mecanizado que sigue al proceso de inyección. A continuación, cada eslabón se termina individualmente a mano para otorgarle su textura satinada. La creación de un brazalete de Alta Relojería es exigente. Si el ajuste de los elementos es demasiado flojo, el brazalete quedará suelto; si al contrario está demasiado apretado, existe el riesgo de que se bloquee. Por tanto, los márgenes de tolerancia deben ser estrictos. Uno a uno, los eslabones se miden, verifican y colocan cuidadosamente para garantizar un ajuste adecuado. Un pasador de metal recorre el brazalete para conectar los eslabones, ya sean metálicos o cerámicos. Generalmente, la forma de los pasadores es redonda en casi todos los brazaletes. En el caso del Bathyscaphe cerámico, la construcción de Blancpain es más sofisticada. Los pasadores tienen una forma patentada de leva que ayuda a garantizar un rango adecuado de flexión al brazalete terminado.
Los biseles cerámicos de Blancpain presentan sus propios desafíos. Tomemos, por ejemplo, el bisel del 70th Anniversary Act 3. Cuenta con un gran índice triangular a las 12 enpunto, números a las 3, 6y 9 horas e índices adheridos en cada marca de 5 minutos. Aunque las hendiduras para las marcas están cortadas con láser, el re- llenado se realiza a mano. El triángulo grande es particularmente difícil ya que la aplicación del material debe ser uniforme en toda su superficie, que es relativamente grande. Utilizando un microscopio binocular para garantizar la uniformidad, el Super-LumiNova se aplica a mano. De manera similar, las marcas del bisel del Bathyscaphe Chronographe también se realizan a mano. Aunque el artesano cuenta con la ayuda de un aparato específicamente diseñado que puede dosificar con precisión cantidades de material de marcado, queda a criterio del especialista realizar los ajustes más minuciosos. Por ejemplo, se necesita menos material para el número 1 que para el 4.
Aunque es cierto que en Blancpain no pensaron en las mandíbulas de un pastor alemán cuando desarrollaron las cajas de cerámica de su Bathyscaphe, así como del resto de los componentes cerámicos, na- die puede negar que tuvieron muy presentes las virtudes de este material: la dureza, la resistencia a los arañazos, la ligereza, la portabilidad sobre la piel y la amplia pa- leta de colores que ofrece.